Zapraszamy do kolejnej części naszej serii case study, która skupi się na zadaniu: „optymalizacja layoutu” w produkcji mebli. Dowiedz się, jak nowoczesne podejścia do planowania przestrzennego mogą przyczynić się do zwiększenia efektywności operacyjnej oraz podniesienia jakości produkowanych mebli.
Opis przypadku
Nasz klient to średniej wielkości firma specjalizująca się w produkcji wysokiej jakości mebli drewnianych. Firma działa na rynku od ponad 20 lat i cieszy się uznaniem zarówno na rynku krajowym, jak i zagranicznym. Produkcja rozpoczyna się od przyjęcia surowego drewna, które jest przecinane przy użyciu piły tarczowej na mniejsze elementy. Następnie te elementy są obrabiane na obrabiarkach CNC, gdzie otrzymują odpowiednie frezowania, wycięcia i wykończenia. Ponadto po obróbce na CNC, detale trafiają na stanowiska montażowe, gdzie rzemieślnicy składają meble z gotowych komponentów. Dodatkowo cały proces produkcji jest ściśle nadzorowany pod kątem jakości, aby zapewnić zgodność z wysokimi standardami firmy.
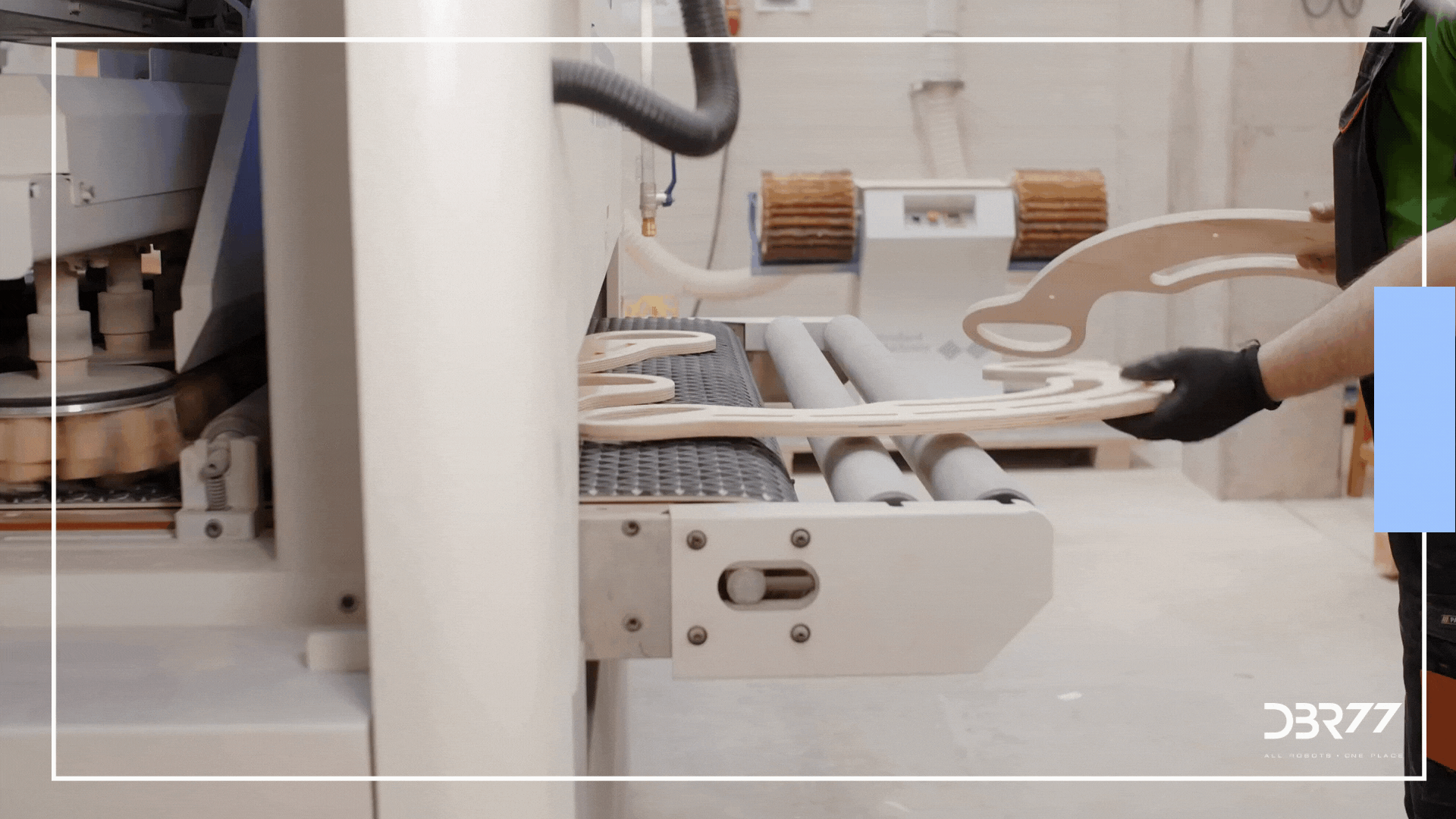
Opis zadania – optymalizacja layoutu
Naszym głównym wyzwaniem było usprawnienie obecnego layoutu produkcyjnego i magazynowego, który nie odpowiadał dynamicznemu środowisku produkcji. Złożoność i różnorodność produkowanych artykułów powodowały powolny przepływ materiałów oraz informacji, co negatywnie wpływało na efektywność operacyjną. Dodatkowo, brak odpowiedniego buforowania materiałów i gotowych wyrobów ograniczał elastyczność produkcji i zwiększał podatność na opóźnienia.

Zrealizowane prace
1. Budowa Bliźniaka Cyfrowego:
- Stworzenie cyfrowego bliźniaka odwzorowującego obecny layout produkcyjny i magazynowy.
- Symulacja przepływu materiałów.
- Opracowanie nowego layoutu produkcyjnego i magazynowego.
2. Projektowanie nowego layoutu:
- Wykorzystanie AI do identyfikacji kluczowych obszarów wymagających optymalizacji.
- Opracowanie nowych propozycji layoutów, uwzględniających złożoność i różnorodność produkowanych artykułów, wspomagane przez AI.
- Wybór optymalnego rozwiązania layoutowego, uwzględniającego specyficzne możliwości firmy przez specjalistów.
- Symulacja wybranego wariantu layoutu za pomocą cyfrowego bliźniaka DBR77.
Wyniki i wnioski – optymalizacja layoutu
Implementacja nowego layoutu za pomocą cyfrowego bliźniaka DBR77 oraz wykorzystanie aglorytmów AI przyniosła widoczne rezultaty:
- Redukcja kapitału obrotowego: Zrezygnowanie z bufora spowodowało ograniczenie poziomu kapitału obrotowego o kwotę 300 tysięcy złotych.
- Redukcja kosztów wydziałowych: Koszty wydziałowe zostały obniżone o 14%, co przyczyniło się do ogólnej redukcji kosztów operacyjnych.
- Redukcja kosztów pracy bezpośredniej: Dzięki optymalizacji layoutu, udało się również zmniejszyć zapotrzebowanie na pracę bezpośrednią o 1,5 etatu.
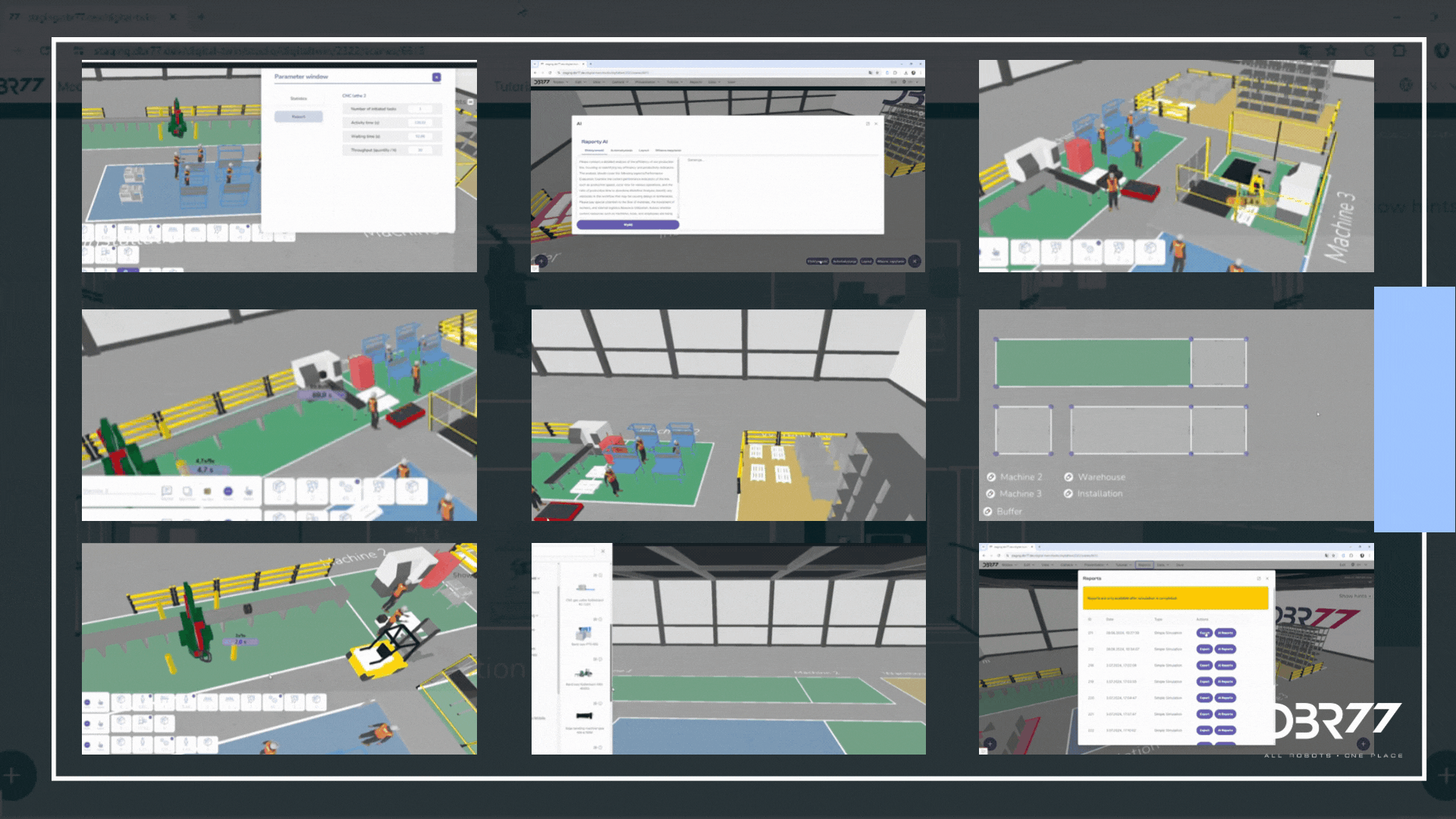
Korzyści dla firmy
Wdrożenie technologii cyfrowego bliźniaka oraz wsparcie AI w procesie projektowania layoutu przyniosło wymierne korzyści, w tym redukcję kosztów i czasu. Dodatkowo umożliwiło firmie lepsze dostosowanie się do dynamicznych wymagań rynkowych, zwiększając jej konkurencyjność. Odwzorowanie obszaru produkcyjnego zajęło kilka dni, jednak dalsze działania optymalizacyjne z wykorzystaniem sztucznej inteligencji przebiegły w czasie liczonym w sekundach, a nie dniach.
Wnioski te potwierdzają, że wykorzystanie zaawansowanych technologii cyfrowych jest kluczowe dla nowoczesnych procesów produkcyjnych i magazynowych, umożliwiając szybką reakcję na zmiany oraz ciągłe doskonalenie efektywności operacyjnej.
Dlaczego Bliźniak Cyfrowy jest optymalnym rozwiązaniem?
1. Szybka możliwość odwzorowania procesu
Bliźniak cyfrowy pozwala na szybkie i dokładne odtworzenie rzeczywistego procesu produkcyjnego w wirtualnym środowisku. Dzięki zaawansowanym narzędziom do modelowania i wizualizacji, procesy mogą być odwzorowane z wysoką precyzją, co umożliwia lepsze zrozumienie i analizę ich funkcjonowania. Szybkie odwzorowanie skraca czas potrzebny na planowanie i implementację, co jest kluczowe w dynamicznych i konkurencyjnych rynkach.
2. Wykorzystanie algorytmów AI
Wykorzystanie algorytmów AI umożliwia jeszcze bardziej zaawansowane analizy danych oraz automatyzację procesów decyzyjnych. Ponadto algorytmy AI wpierają w identyfikacji wzorców, optymalizacji parametrów oraz szybkiej adaptacji do zmieniających się warunków rynkowych, co zwiększa efektywność operacyjną i konkurencyjność przedsiębiorstwa.
3. Łatwość aktualizacji założeń i wygenerowania nowych alternatywnych linii pobrań materiałowych
Bliźniak cyfrowy oferuje elastyczność w aktualizacji założeń i tworzeniu nowych alternatywnych scenariuszy. W miarę jak zmieniają się warunki produkcyjne, założenia mogą być łatwo modyfikowane, a nowe alternatywne linie pobrań materiałowych mogą być szybko generowane. Dlatego zdolność do adaptacji pozwala na bieżąco reagować na zmiany w środowisku produkcyjnym, co zwiększa efektywność i elastyczność operacyjną.
PODSUMOWANIE
Podsumowując, wdrożenie Cyfrowego bliźniaka DBR77 i sztucznej inteligencji (AI) przyniosło znaczące korzyści dla firmy, umożliwiając precyzyjne odwzorowanie procesów produkcyjnych i magazynowych oraz szybsze reagowanie na zmiany i optymalizację operacyjną. Integracja z AI automatyzowała analizę danych, wspierając trafniejsze decyzje zarządcze. W związku z tym efektem było istotne obniżenie kosztów operacyjnych i czasu przemieszczania materiałów i pracowników, co zwiększyło efektywność i elastyczność firmy oraz umocniło jej pozycję na dynamicznym rynku.
Zobacz też film o Bliźniaku Cyfrowym z konferencji DBR77 „(R)ewolucja Przemysłowa”: