Bliźniaki cyfrowe (Digital Twins) obiektów i procesów, stają się ważnym elementem ich optymalizacji oraz poprawy efektywności. Dla firm produkcyjnych i logistycznych, przed wdrożeniem bliźniaka, czyli cyfrowej repliki zakładu, konieczne jest ustalenie jaka infrastruktura i nakłady finansowe są niezbędne do zapewnienia funkcjonowania dla tego rozwiązania. Dlatego warto wskazać 7 rzeczy, które należy wiedzieć przed podjęciem decyzji o implementacji bliźniaka cyfrowego w Twoim zakładzie.
I. Znalezienie optymalnej ścieżki wdrożenia
Wdrożenie cyfrowego bliźniaka zakładu produkcyjnego to proces, który wymaga dokładnego planowania i strategicznego podejścia. Nie jest to jednorazowe działanie, lecz raczej ciągła podróż w kierunku cyfryzacji i automatyzacji. Aby osiągnąć sukces, zarząd firmy powinien przyjąć metodykę stopniowego wdrażania, która zaczyna się od kluczowych obszarów produkcyjnych.
Jakie kroki pomogą w znalezieniu optymalnej ścieżki wdrożenia? Jakie pozwolą na skuteczne wdrożenie rozwiązania?
- Analiza potrzeb: zidentyfikuj kluczowe obszary, które najbardziej skorzystają na wdrożeniu, aby określić priorytety przed wdrożeniem bliźniaka.
- Wybór obszarów do pilotażu: skup się na specyficznych segmentach dla pierwszych testów, minimalizując zakłócenia operacyjne.
- Budowa zespołu: utwórz multidyscyplinarny zespół ekspertów do nadzorowania procesu wdrożenia.
- Implementacja i testowanie: rozpocznij wdrażanie w wybranych obszarach, monitorując postępy i dostosowując procesy.
- Ocena i skalowanie: oceń wyniki pilotażu, identyfikując najlepsze praktyki i możliwości rozszerzenia projektu.
- Szkolenie personelu: zapewnij szkolenia, aby personel mógł skutecznie wykorzystać nowe technologie.
- Iteracyjne ulepszenia: traktuj wdrożenie jako ciągły proces, który wymaga regularnych aktualizacji i optymalizacji.
Takie podejście umożliwia stopniową adaptację do nowych rozwiązań, minimalizując ryzyko i maksymalizując korzyści płynące z cyfrowej transformacji.
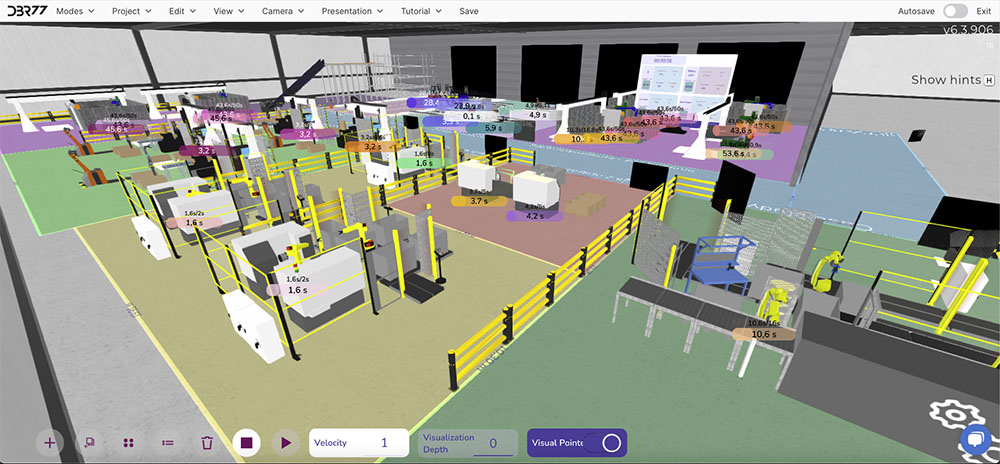
II. Zrozumienie kluczowych procesów produkcyjnych przed wdrożeniem bliźniaka
Przed rozpoczęciem wdrażania Digital Twin, firma musi dokładnie zrozumieć kluczowe procesy produkcyjne w swojej organizacji. To obejmuje analizę zarówno głównych, jak i pobocznych etapów produkcji oraz identyfikację obszarów, w których bliźniak cyfrowy fabryki może przynieść najwięcej korzyści.
Przykłady analizy głównych etapów produkcji:
- Analiza przepływu materiału: należy zrozumieć, jak poszczególne komponenty przemieszczają się przez proces produkcyjny. Określamy wszystkie źródła materiałów, punkty przepływu oraz miejsca, w których materiały mogą być magazynowane lub przetwarzane.
- Analiza strumienia informacji: kluczowe jest również określenie najważniejszych danych produkcyjnych oraz tego, w jaki sposób są one analizowane i przetwarzane. Prawidłowy przepływ informacji na wszystkich poziomach zarządzania jest istotnym elementem prawidłowego funkcjonowania nowoczesnego zakładu produkcyjnego.
Przykłady analizy pobocznych etapów produkcji:
- Analiza konserwacji: weryfikacja sposobu i czasu konserwacji maszyn oraz urządzeń.
- Analiza jakości: kontrola jakości to kolejny ważny element procesu produkcyjnego. Istotnym jest zidentyfikowanie wszystkich produktów, które wymagają testów jakości oraz doprecyzowanie częstotliwości testów oraz ich sposobu.
- Analiza bezpieczeństwa: odnosi się szczególnie do bezpieczeństwa pracowników oraz środowiska. Wskazanie wszystkich zagrożeń dla bezpieczeństwa procesu produkcyjnego jest istotne, aby minimalizować ryzyko oraz ewentualne straty.
III. Wsparcie zespołu projektowego przed wdrożeniem bliźniaka
Wdrożenie bliźniaka cyfrowego zakładu produkcyjnego to kompleksowe przedsięwzięcie, które wymaga ścisłej współpracy między różnymi działami organizacji, w tym IT, produkcją i finansami. Każdy członek zespołu staje się istotną jednostką w zapewnieniu efektywnego wsparcia dla pozostałych członków zespołu projektowego. Dzięki temu można zapewnić płynność procesu wdrożenia.
Istotne obszary współpracy to:
Zarządzanie budżetem
Skuteczne wdrożenie bliźniaka cyfrowego fabryki wiąże się najczęściej z istotnymi kosztami. Konieczne jest zapewnienie, aby firma dysponowała wystarczającym budżetem, aby skutecznie zrealizować projekt. Warto rozważyć opcje, które optymalizują koszty (np. wykorzystanie modelu subskrypcyjnego i dostępu online do gotowego środowiska. Takim rozwiązaniem jest Bliźniak Cyfrowy DBR77).
Zapewnienie dostępu do istotnych danych
Zespół projektowy musi mieć swobodny dostęp do danych produkcyjnych, niezbędnych do konstrukcji i integracji bliźniaka cyfrowego. Wszystkie jednostki organizacji powinny zagwarantować, że te dane są ustrukturyzowane, aktualne i łatwo dostępne dla zespołu. Służyć temu może wdrożenie systemu IoT w fabryce, który zbiera bieżące dane produkcyjne. Niewątpliwie ważna jest również rola oprogramowania zarządczego jak ERP czy MES. Dostęp do uporządkowanych danych pozwala na prawidłową optymalizację procesów.
Szkolenie i rozwój umiejętności
Wdrożenie bliźniaka cyfrowego wymaga nowych umiejętności i wiedzy. Managerowie powinni zainwestować w odpowiednie szkolenia dla członków zespołu projektowego. Dzięki temu można zabezpieczyć sukces inwestycji w to cyfrowe rozwiązanie. Ponadto, można korzystać z wszystkich możliwości i ułatwień, jakie daje to rozwiązanie.
Wsparcie kierownictwa
Realizacja projektu bliźniaka cyfrowego jest przedsięwzięciem wymagającym zaangażowania kierownictwa z wszystkich obszarów działania organizacji. Zarząd firmy powinien działać aktywnie w celu zapewnienia silnego wsparcia. Bez wątpienia stanowi to kluczowy czynnik sukcesu projektu. Odpowiednie zarządzanie tymi obszarami wsparcia będzie decydujące dla efektywnego i udanego wdrożenia cyfrowego klonu fabryki.
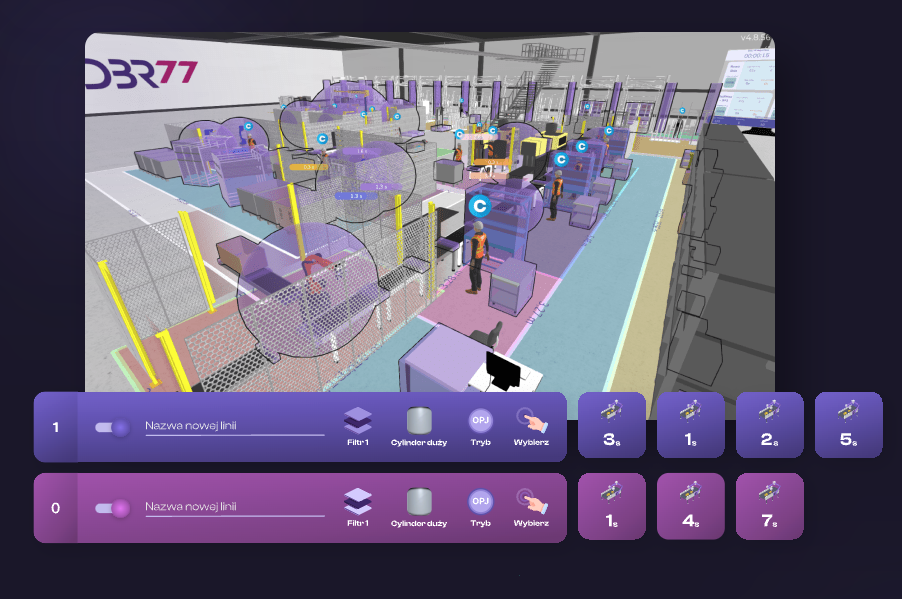
IV. Kluczowe technologie i platformy
Zanim przystąpimy do procesu wdrożenia, konieczne jest pełne zrozumienie kluczowych technologii i platform, które będą wykorzystane do stworzenia bliźniaka cyfrowego zakładu produkcyjnego. Niezbędne jest przeprowadzenie szczegółowej analizy narzędzi do zbierania danych, systemów analizy danych oraz interfejsów użytkownika. Niewątpliwie to one odgrywają ważną rolę w efektywnym monitorowaniu i zarządzaniu procesami produkcyjnymi.
- Narzędzia do zbierania danych: sensory i urządzenia IoT (Internet of Things) są kluczowe w automatycznym zbieraniu danych z maszyn i procesów produkcyjnych. Przykładowo są to sensory temperatury, wilgotności, ciśnienia czy czujniki wibracji, które dostarczają danych w czasie rzeczywistym. Pośród nich można wymienić systemy SCADA (Supervisory Control And Data Acquisition), które pozwalają na monitorowanie i kontrolę procesów przemysłowych na dużą skalę, zapewniając cenny wgląd w działanie całego zakładu.
- Systemy analizy danych: platformy Big Data i narzędzia do przetwarzania danych takie jak Apache Hadoop czy Spark, które umożliwiają przetwarzanie i analizę ogromnych zbiorów danych, identyfikując wzorce i anomalie. Dzięki temu mogą wskazywać na potencjalne problemy produkcyjne.
- Oprogramowanie do symulacji i modelowania pozwala na tworzenie zaawansowanych modeli cyfrowych zakładu. W ten sposób umożliwia symulacje różnych scenariuszy operacyjnych i optymalizację procesów.
- Interfejsy użytkownika – dashboards i aplikacje mobilne. Niezbędne dla wygodnego dostępu do danych i analiz w czasie rzeczywistym. Przykładem mogą być interaktywne pulpity nawigacyjne, które prezentują kluczowe wskaźniki wydajności (KPIs). W ten sposób umożliwiają szybką reakcję na zmiany w procesach produkcyjnych.
- Rozwiązania w zakresie Augmented Reality (AR) i Virtual Reality (VR). Mogą być wykorzystywane do wizualizacji procesów i pomagają w szkoleniu pracowników. Oferują interaktywne doświadczenia zbliżone do realnych warunków pracy.
- Integracja systemów middleware i API (Application Programming Interfaces). Niezbędne do integracji różnych systemów i aplikacji. Pozwalają na płynną wymianę danych między narzędziami do zbierania danych, systemami analizy, a interfejsami użytkownika. Dzięki temu zapewniają spójność i aktualność informacji.
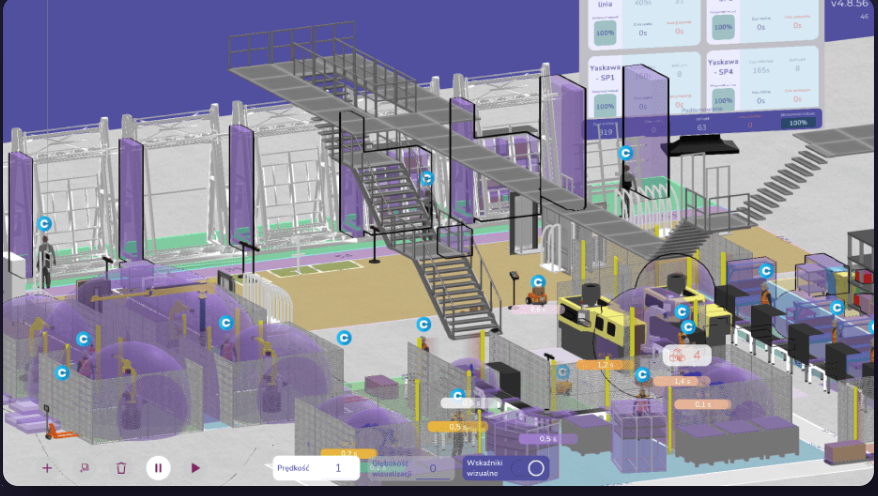
V. Bezpieczeństwo danych przed wdrożeniem bliźniaka na produkcji
Bezpieczeństwo danych jest kolejnym ważnym elementem projektów związanych z cyfrowym klonem fabryki. Zespół projektowy musi być świadomy potencjalnych zagrożeń, związanych z gromadzeniem i przetwarzaniem danych produkcyjnych. Konieczne jest zapewnienie odpowiednich środków bezpieczeństwa, aby chronić wrażliwe informacje przed nieautoryzowanym dostępem.
Jakie są przykłady potencjalnych zagrożeń związanych z gromadzeniem i przetwarzaniem danych produkcyjnych?
- Dane produkcyjne mogą być cennym celem dla hakerów. Mogą one zostać wykorzystane do kradzieży informacji o produktach, procesach produkcyjnych lub klientach.
- Dane produkcyjne mogą zostać zmodyfikowane w celu wprowadzenia w błąd lub wyrządzenia szkody firmie.
- Utrata danych produkcyjnych może spowodować poważne problemy, takie jak przerwy w produkcji lub obniżenie jakości produktów.
Jakie środki bezpieczeństwa można podjąć, aby chronić dane produkcyjne?
- Dostęp do danych produkcyjnych należy ograniczyć do autoryzowanych użytkowników. Należy stosować silne hasła i uwierzytelnianie dwuskładnikowe.
- Dane produkcyjne należy szyfrować, aby uniemożliwić nieautoryzowanemu dostępowi.
- Kopie zapasowe danych produkcyjnych należy wykonywać regularnie, aby w przypadku utraty danych można było je odzyskać.
VI. Proaktywne zarządzanie ryzykiem przed wdrożeniem bliźniaka
Każdy projekt niesie ze sobą pewne ryzyko. Zanim rozpocznie się implementację, zespół projektowy powinien dokładnie ocenić potencjalne zagrożenia i przygotować plan zarządzania ryzykiem. To obejmuje identyfikację potencjalnych przeszkód oraz opracowanie strategii ich minimalizacji.
Przyjrzyjmy się przypadkowi z rynku, gdzie firma produkująca opakowania foliowe, przy realizacji nowej linii produkcyjnej, zidentyfikowała potencjalne opóźnienia w dostawach surowców. Dzięki wcześniejszej analizie, zastosowano strategię awaryjną poprzez zdywersyfikowanie dostawców i stworzenie rezerwowych magazynów. Rezultat? Projekt utrzymany w harmonogramie, a ryzyko przekształcone w szansę. To potwierdza, że proaktywne zarządzanie ryzykiem to klucz do sukcesu w dynamicznym świecie produkcji.
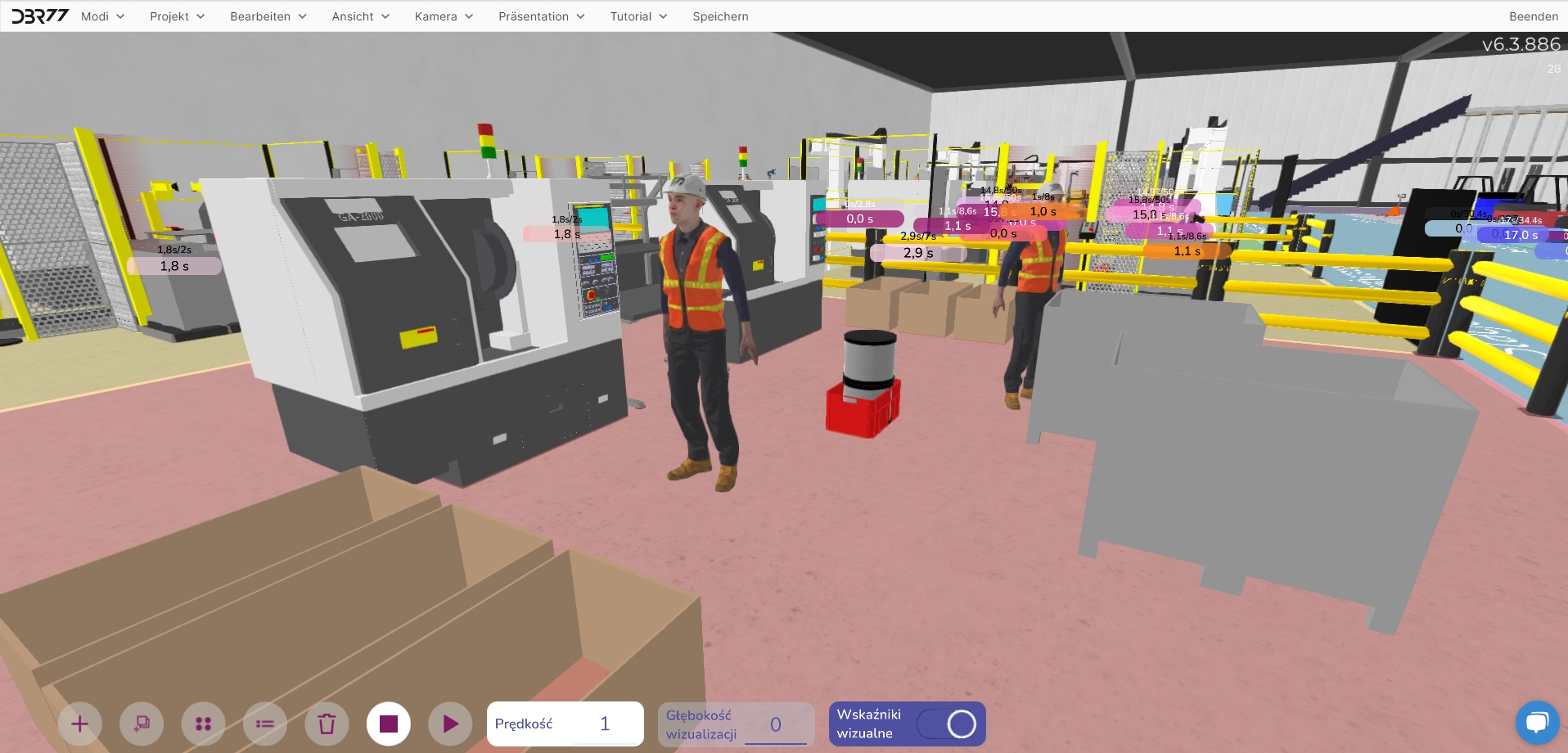
VII. Ciągłe monitorowanie efektów
Po pomyślnym wdrożeniu bliźniaka cyfrowego zakładu produkcyjnego, niezbędnym krokiem do pełnego wykorzystania jego potencjału jest ciągłe monitorowanie i analiza wyników. Monitorowanie to nie tylko zwykłe śledzenie parametrów operacyjnych, ale przede wszystkim zrozumienie, jak cyfrowy bliźniak wpływa na wydajność i efektywność produkcji.
Jakie działania są ważne w tym kontekście?
Zbieranie i analiza danych w czasie rzeczywistym
Wykorzystanie zaawansowanych narzędzi analitycznych do ciągłego zbierania danych z produkcji umożliwia szybkie wykrywanie wszelkich odchyleń od normy. Dzięki temu można natychmiast reagować na pojawiające się problemy.
- Jak zrealizować? Zaimplementuj systemy IoT (Internet of Things) do monitorowania maszyn i procesów w czasie rzeczywistym. Użyj oprogramowania do analizy danych, które może przetwarzać wielkie zbiory danych i wyciągać z nich wnioski.
- Przykłady monitorowania: Zastosuj dashboardy analityczne pokazujące kluczowe wskaźniki wydajności (KPIs) takie jak czas cyklu, wykorzystanie maszyn, i jakość produkcji, umożliwiające szybką reakcję na anomalie.
Współpraca międzydziałowa
Ciągła współpraca między członkami zespołu wdrażającego, użytkownikami systemu, inżynierami procesu i analitykami danych jest fundamentem efektywnego monitorowania. Komunikacja i wymiana informacji pozwalają na holistyczne podejście do analizy wyników.
- Jak zrealizować? Organizuj regularne spotkania międzydziałowe z udziałem przedstawicieli produkcji, IT, utrzymania ruchu i zarządzania jakością. Użyj platform do współpracy online, aby ułatwić wymianę informacji.
- Przykłady monitorowania: utwórz grupę roboczą na platformie do współpracy, gdzie zespół może na bieżąco dzielić się aktualizacjami, wyzwaniami i sukcesami projektu.
Ocena realizacji celów
Regularne przeglądy wyników z zastosowaniem wyznaczonych wskaźników efektywności (KPIs) pozwalają ocenić, czy i w jakim stopniu cele projektu zostały osiągnięte. To również moment na weryfikację czy założenia dotyczące korzyści z wdrożenia cyfrowego bliźniaka są spełnione.
- Jak zrealizować? Ustal konkretne, mierzalne, osiągalne, relewantne i czasowo określone (SMART) cele dla projektu. Wykorzystaj narzędzia do śledzenia postępów i porównywania rzeczywistych wyników z oczekiwaniami.
- Przykłady monitorowania: monitoruj wskaźniki takie jak redukcja czasu przestoju, zwiększenie wydajności linii produkcyjnej czy poprawa jakości produktu, porównując je z celami projektu.
Dokonywanie korekt i optymalizacja procesów
Na podstawie analizy danych i feedbacku użytkowników, konieczne może być dokonanie korekt w strategii działania lub bezpośrednio w procesach produkcyjnych. Optymalizacja może dotyczyć zarówno aspektów technologicznych, jak i organizacyjnych.
- Jak zrealizować? Zastosuj metodykę Lean Manufacturing do identyfikacji marnotrawstwa i nieefektywności. Wykorzystaj techniki takie jak Kaizen dla ciągłego doskonalenia.
- Przykłady monitorowania: organizuj regularne warsztaty Kaizen, aby identyfikować i implementować ulepszenia w procesach.
Iteracyjne ulepszanie
Monitorowanie efektów jest procesem ciągłym, który nie kończy się na jednorazowej ocenie. Dzięki regularnym aktualizacjom i ulepszeniom, możliwe jest nieustanne doskonalenie wydajności i efektywności operacyjnej zakładu.
- Jak zrealizować? Ustal cykle przeglądów projektu, podczas których analizowane są zebrane dane i podejmowane decyzje o dalszych działaniach. Zastosuj zwinne metody zarządzania projektami.
- Przykłady monitorowania: użyj retrospektyw projektowych do analizy, co działało dobrze, a co wymaga poprawy i planuj kolejne kroki w oparciu o te wnioski.
Szkolenie i rozwój personelu
Wdrażanie nowych rozwiązań i technologii wymaga również ciągłego szkolenia personelu. Zapewnienie, że wszyscy pracownicy są na bieżąco z możliwościami oferowanymi przez cyfrowego bliźniaka, jest kluczowe dla maksymalizacji korzyści z jego wdrożenia.
- Jak zrealizować? Opracuj program szkoleniowy, który uwzględnia zarówno wiedzę teoretyczną, jak i praktyczne umiejętności obsługi nowych technologii. Zorganizuj warsztaty, webinary i sesje mentoringowe.
- Przykłady monitorowania: monitoruj postępy pracowników w ramach szkoleń poprzez testy i oceny praktyczne, dostosowując program szkoleniowy do indywidualnych potrzeb rozwojowych.
Podsumowanie
Podsumowując, przed podjęciem decyzji związanej z wdrożeniem bliźniaka zakładu produkcyjnego, należy aktywnie uczestniczyć w całym procesie planowania i analizy przedsięwzięcia. Zrozumienie kluczowych aspektów technologicznych, procesowych i finansowych jest kluczowe dla osiągnięcia sukcesu w zakresie optymalizacji produkcji. Wdrożenie cyfrowego bliźniaka fabryki to nie tylko inwestycja w technologię, ale również strategiczny krok w kierunku zwiększenia efektywności i konkurencyjności firmy.
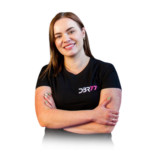
Autor:
Dorota Drzewiecka, DBR 77 Robotics
Kontakt:
e-mail: dorota.drzewiecka@dbr77.com