To kolejny artykuł z naszej serii o IoT w produkcji i jego praktycznych zastosowaniach w przemyśle. W poprzednich tekstach omawialiśmy monitorowanie maszyn i analizę danych produkcyjnych. Dziś skupimy się na jednym z kluczowych wskaźników efektywności – czasie cyklu. Jak dokładnie go mierzyć i jak system IoT DBR77 pomaga w jego optymalizacji?
Cel artykułu
Celem niniejszego artykułu jest przedstawienie systemu czujników IoT DBR77 jako sposobu na automatyczne zbieranie informacji o czasach cykli procesów oraz ich optymalizację.
Definicja i wpływ na efektywność operacyjną
Czas cyklu to czas potrzebny na wykonanie pełnego procesu produkcyjnego jednej jednostki produktu na danym stanowisku. Jego precyzyjny pomiar pozwala na identyfikację strat, ograniczenie nieefektywnych operacji i lepszą synchronizację pracy maszyn. Dzięki temu firmy mogą eliminować nadmierne przestoje oraz poprawiać wydajność całego procesu produkcyjnego.
Wpływ na planowanie produkcji i optymalizację procesów
Dane o czasie cyklu są niezbędne do efektywnego zarządzania produkcją. Pozwalają lepiej planować harmonogramy, minimalizować straty wynikające z nieprzewidzianych przestojów oraz optymalizować wykorzystanie zasobów. Dzięki systemowi IoT DBR77 możliwe jest automatyczne zbieranie i analiza danych. Umożliwia to wprowadzanie ulepszeń w czasie rzeczywistym, zwiększając konkurencyjność i efektywność operacyjną przedsiębiorstwa.
Podstawy technologii czujników w produkcji
Rola czujników w automatyzacji pomiarów
Współczesne zakłady produkcyjne stawiają na automatyzację procesów, a jednym z kluczowych elementów tej transformacji są czujniki. Odgrywają one istotną rolę w monitorowaniu produkcji, umożliwiając precyzyjny pomiar czasu cyklu bez ingerencji człowieka. Dzięki temu eliminowane są błędy ludzkie wynikające z niedokładności, zmęczenia czy subiektywnej oceny operatorów.
Czujniki umożliwiają zbieranie danych w czasie rzeczywistym, co pozwala na szybką analizę i reagowanie na wszelkie odstępstwa od normy. Informacje te mogą być wykorzystywane nie tylko do optymalizacji poszczególnych operacji, ale także do wdrażania metod predykcyjnej konserwacji, które pomagają unikać awarii maszyn i minimalizować przestoje.
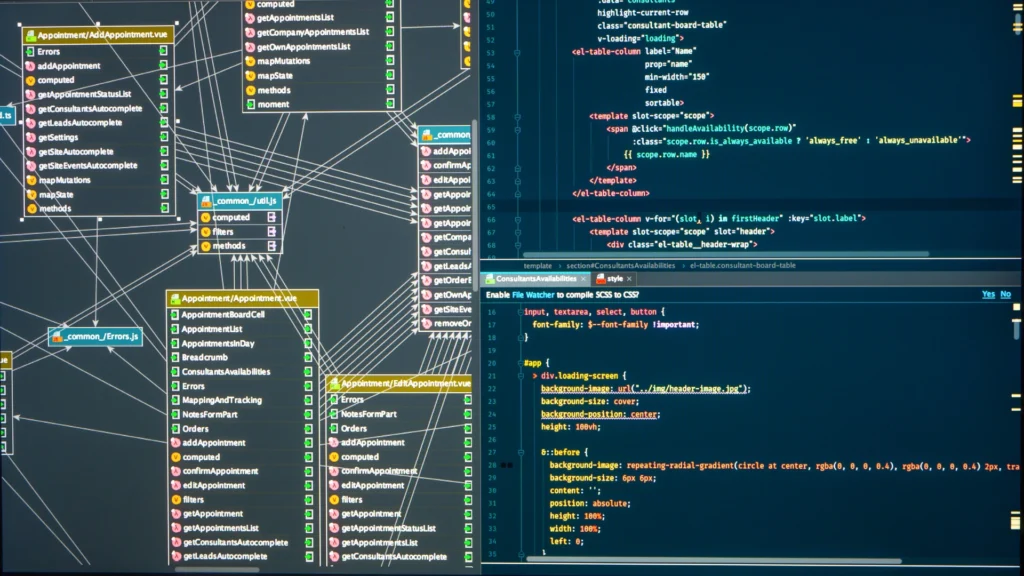
Integracja czujników z systemami monitorowania (IoT, MES, ERP, cyfrowy bliźniak)
Współczesne przedsiębiorstwa coraz częściej korzystają z kompleksowych systemów zarządzania produkcją, które pozwalają na integrację danych z różnych źródeł. Czujniki mogą być podłączone do systemów takich jak:
- IoT (Internet of Things) – umożliwia przesyłanie danych z czujników do centralnych baz w chmurze i analizowanie ich w czasie rzeczywistym. System IoT DBR77 pozwala na kompleksowe monitorowanie urządzeń i procesów produkcyjnych, dostarczając kluczowych informacji o efektywności operacyjnej oraz umożliwiając automatyczne reagowanie na zmiany w czasie rzeczywistym.
- MES (Manufacturing Execution System) – system zarządzania operacjami produkcyjnymi, który pomaga w monitorowaniu i optymalizacji procesów.
- ERP (Enterprise Resource Planning) – system zarządzania zasobami przedsiębiorstwa, który pozwala na synchronizację danych o produkcji z innymi działami firmy, takimi jak logistyka czy finanse.
- Cyfrowy bliźniak – wirtualny model rzeczywistego zakładu produkcyjnego, który pozwala na testowanie różnych scenariuszy optymalizacyjnych bez wpływu na rzeczywisty proces. Dzięki technologii cyfrowego bliźniaka oferowanej przez system IoT DBR77 przedsiębiorstwa mogą precyzyjnie symulować zmiany w procesach produkcyjnych i przewidywać potencjalne zakłócenia, co pozwala na jeszcze bardziej efektywne zarządzanie produkcją.
Dzięki integracji czujników z tymi systemami możliwe jest kompleksowe monitorowanie produkcji, identyfikacja potencjalnych problemów oraz wdrażanie działań zapobiegawczych w oparciu o rzeczywiste dane.
Metodologia wyznaczania czasu cyklu
Aby skutecznie wyznaczyć czas cyklu, kluczowe jest zidentyfikowanie jednego, powtarzalnego w trakcie realizacji procesu zdarzenia lub czynności, które można precyzyjnie zmierzyć. W miejscu jego występowania instaluje się czujnik, który automatycznie rejestruje moment rozpoczęcia i zakończenia danego etapu produkcji.
Przykład 1: Proces wtryskiwania tworzyw sztucznych
W przypadku maszyn wtryskowych czas cyklu można wyznaczyć na podstawie operacji wyciągania gotowego elementu z formy. Ponieważ proces ten odbywa się w każdym cyklu produkcji, zamontowanie czujnika na ramieniu robota odbierającego produkt pozwala na precyzyjne określenie momentu zakończenia jednego cyklu i rozpoczęcia kolejnego. Rejestrowane dane umożliwiają analizę efektywności procesu, identyfikację opóźnień oraz ocenę stabilności pracy maszyny.
Przykład 2: Stanowisko manualne
W procesie ręcznej produkcji, gdzie operator wyciąga komponenty z pojemnika i montuje je w produkcie końcowym, czas cyklu można określić poprzez monitorowanie momentu sięgnięcia po nowy element. Czujnik optyczny lub zbliżeniowy zamontowany przy pojemniku rejestruje każdorazowe pobranie elementu, co pozwala na dokładne określenie czasów między kolejnymi operacjami. Taki pomiar pozwala na ocenę wydajności operatora, optymalizację ergonomii stanowiska oraz identyfikację potencjalnych strat czasowych.
Dzięki zastosowaniu tej metody firmy mogą lepiej analizować swoje procesy produkcyjne, identyfikować wąskie gardła i podejmować decyzje mające na celu poprawę efektywności operacyjnej.
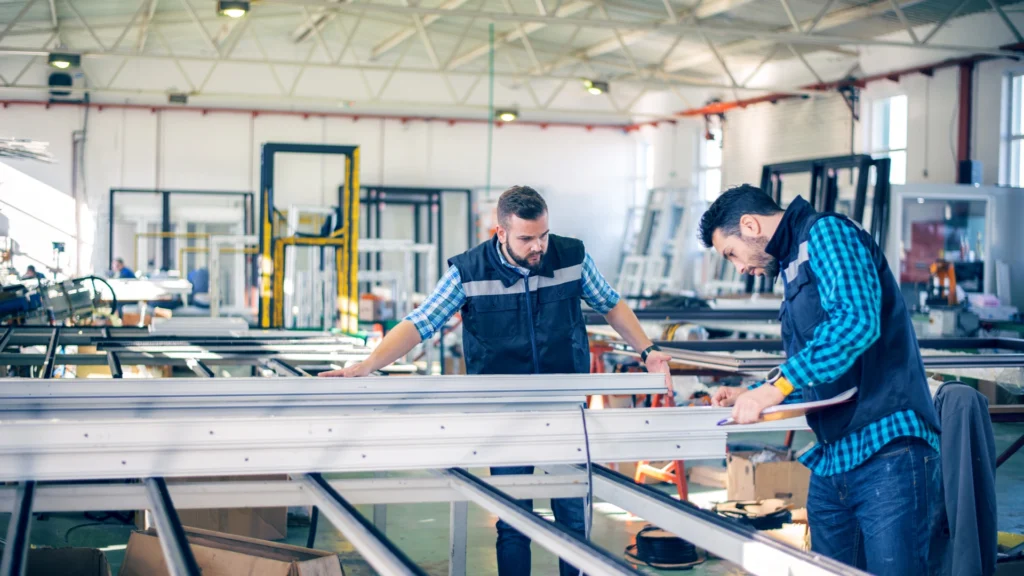
Jakie korzyści daje ta metoda?
Zastosowanie czujników do pomiaru czasu cyklu w procesach produkcyjnych przynosi szereg istotnych korzyści. Przede wszystkim pozwala na zwiększenie dokładności pomiaru, eliminując błędy wynikające z ręcznego monitorowania, które mogą prowadzić do niedokładności w analizie efektywności operacyjnej. Dzięki temu automatyzacja pomiarów zapewnia precyzyjne dane w czasie rzeczywistym. System DBR77 umożliwia ich inteligentną analizę i natychmiastowe wykorzystywanie do optymalizacji produkcji. Przekłada się to na lepszą kontrolę nad przebiegiem procesów.
Dodatkowo metoda ta pozwala na zmniejszenie liczby koniecznych czujników, ponieważ często wystarczy umieszczenie jednego czujnika w kluczowym punkcie, aby uzyskać kompleksowe informacje o przebiegu cyklu. Dzięki temu możliwe jest ograniczenie kosztów instalacji i konserwacji, a jednocześnie utrzymanie wysokiej jakości zbieranych danych.
Największą wartością tej metody jest jednak możliwość analizy i optymalizacji procesów na podstawie rzeczywistych danych. Dostęp do precyzyjnych informacji poprzez system IoT DBR77 umożliwia lepsze planowanie produkcji, identyfikację i eliminację wąskich gardeł oraz skuteczniejsze zarządzanie wydajnością operacyjną. W efekcie przedsiębiorstwa mogą zwiększać swoją konkurencyjność, redukować przestoje i efektywniej wykorzystywać zasoby.
Rodzaje czujników i ich zastosowanie w systemie DBR77
System DBR77 wykorzystuje różnorodne czujniki do monitorowania procesów produkcyjnych. Umożliwiają one automatyzację pomiarów, optymalizację operacji oraz zwiększenie efektywności i niezawodności maszyn. Poniżej przedstawiamy kluczowe typy czujników stosowane w systemie oraz ich znaczenie w zarządzaniu produkcją.
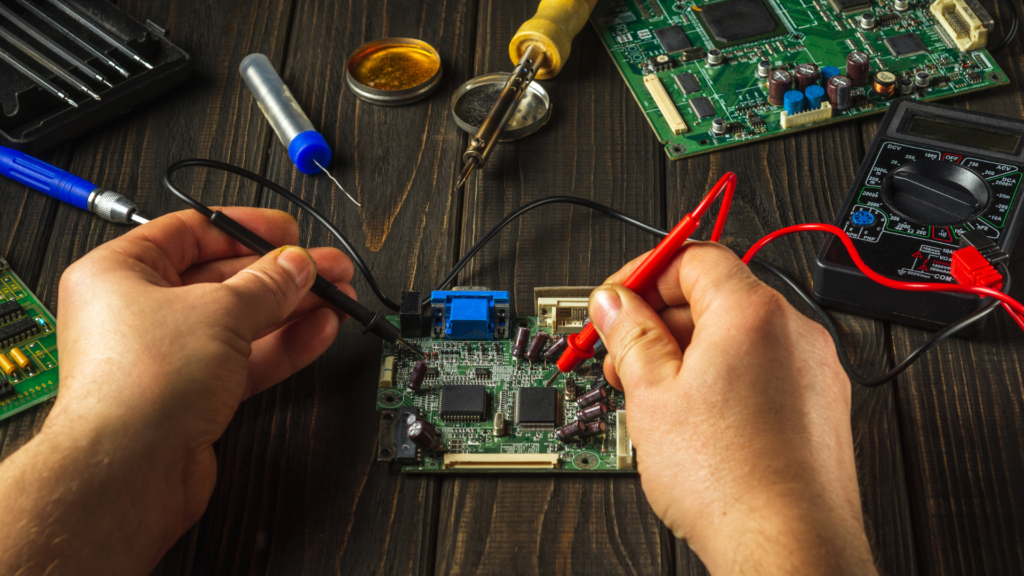
Czujnik zbliżeniowy
Czujniki zbliżeniowe pozwalają na wykrywanie obiektów bez konieczności fizycznego kontaktu. Działają na zasadzie pola magnetycznego, ultradźwięków, podczerwieni lub technologii pojemnościowej, co umożliwia ich zastosowanie w różnych warunkach przemysłowych. Czujniki magnetyczne wykrywają wyłącznie metalowe elementy, podczas gdy czujniki pojemnościowe mogą rejestrować także materiały nieprzewodzące, takie jak tworzywa sztuczne. Ultradźwiękowe i podczerwone wersje sprawdzają się przy pomiarze odległości, co pozwala na dokładne określenie pozycji obiektów.
W systemie DBR77 czujniki zbliżeniowe znajdują zastosowanie w automatyzacji procesów montażowych. Ponadto w wykrywaniu komponentów na taśmach produkcyjnych oraz zabezpieczaniu maszyn przed kolizjami. Dzięki nim system może dynamicznie reagować na zmiany w układzie linii produkcyjnej, co minimalizuje ryzyko błędów i przestojów. Są one również wykorzystywane w systemach wizyjnych do identyfikacji produktów, co usprawnia sortowanie i kontrolę jakości.
Czujnik barierowy
Czujniki barierowe działają na zasadzie wiązki świetlnej przesyłanej między nadajnikiem a odbiornikiem. W momencie przerwania wiązki przez obiekt, system natychmiast rejestruje zdarzenie. Pozwala to na precyzyjne wykrywanie ruchu i obecności produktów na linii produkcyjnej. Dzięki wykorzystaniu podczerwieni lub laserów, czujniki te mogą pracować z wysoką dokładnością, nawet w trudnych warunkach środowiskowych, takich jak duże zapylenie czy intensywne oświetlenie.
W systemie DBR77 czujniki barierowe są stosowane do kontroli przepływu produktów na liniach montażowych i sortujących. Umożliwiają one automatyczne zatrzymywanie i uruchamianie maszyn w zależności od obecności obiektu, co poprawia bezpieczeństwo i optymalizację pracy. Dodatkowo pełnią funkcję ochronną – w przypadku wykrycia ruchu w strefie zagrożenia mogą natychmiast wyłączyć maszynę, zapobiegając potencjalnym wypadkom.
Czujnik wibracyjny
Czujniki wibracyjne monitorują drgania maszyn i konstrukcji przemysłowych, rejestrując ich intensywność oraz częstotliwość. Działają na zasadzie pomiaru sił dynamicznych, które powstają w wyniku ruchu obrotowego i liniowego elementów mechanicznych. Wykorzystują technologię piezoelektryczną lub akcelerometry do wykrywania zmian w normalnym funkcjonowaniu urządzeń, co pozwala na szybkie diagnozowanie problemów.
W systemie DBR77 czujniki wibracyjne pełnią kluczową rolę w predykcyjnej konserwacji maszyn. Analizując zmiany w charakterystyce drgań, system jest w stanie wykrywać wczesne oznaki zużycia elementów mechanicznych, takich jak łożyska czy wały napędowe. Pozwala to na planowanie napraw z wyprzedzeniem i minimalizowanie nieplanowanych przestojów, co znacząco zwiększa efektywność operacyjną zakładów produkcyjnych.
Mierniki energii
Mierniki energii służą do monitorowania zużycia energii elektrycznej w maszynach i urządzeniach przemysłowych. Działają na zasadzie rejestracji kluczowych parametrów, takich jak napięcie, natężenie prądu, pobór mocy oraz współczynnik mocy. Dane są zbierane w czasie rzeczywistym i przesyłane do centralnego systemu analizy. Następnie są wykorzystywane do identyfikacji obszarów o wysokim zużyciu energii oraz optymalizacji pracy maszyn.
W systemie DBR77 mierniki energii odgrywają istotną rolę w zarządzaniu efektywnością energetyczną zakładu. Pozwalają one na identyfikację nieefektywnych procesów i wdrażanie działań mających na celu redukcję strat energii. Monitorowanie zużycia energii w czasie rzeczywistym umożliwia również szybkie reagowanie na nagłe zmiany w poborze mocy. Pomaga to w zapobieganiu przeciążeniom i optymalizacji kosztów operacyjnych.
Przycisk deklaracji operatora
Przycisk deklaracji operatora to manualny interfejs umożliwiający pracownikom rejestrowanie istotnych zdarzeń w systemie produkcyjnym. Może być podłączony do systemu MES lub HMI, co pozwala na natychmiastowe przesyłanie informacji do centralnej bazy danych. Dzięki temu operatorzy mogą zgłaszać rozpoczęcie i zakończenie pracy maszyny, przyczyny przestojów oraz inne istotne zdarzenia wpływające na przebieg produkcji.
W systemie DBR77 przycisk deklaracji operatora pełni kluczową funkcję w analizie czasu pracy i optymalizacji harmonogramów produkcyjnych. Dzięki ręcznej rejestracji statusów pracy można precyzyjnie określić wpływ czynników ludzkich na przestoje i wydajność linii produkcyjnych. Informacje te są wykorzystywane do doskonalenia organizacji pracy oraz wdrażania usprawnień eliminujących zbędne przerwy i poprawiających efektywność operacyjną.
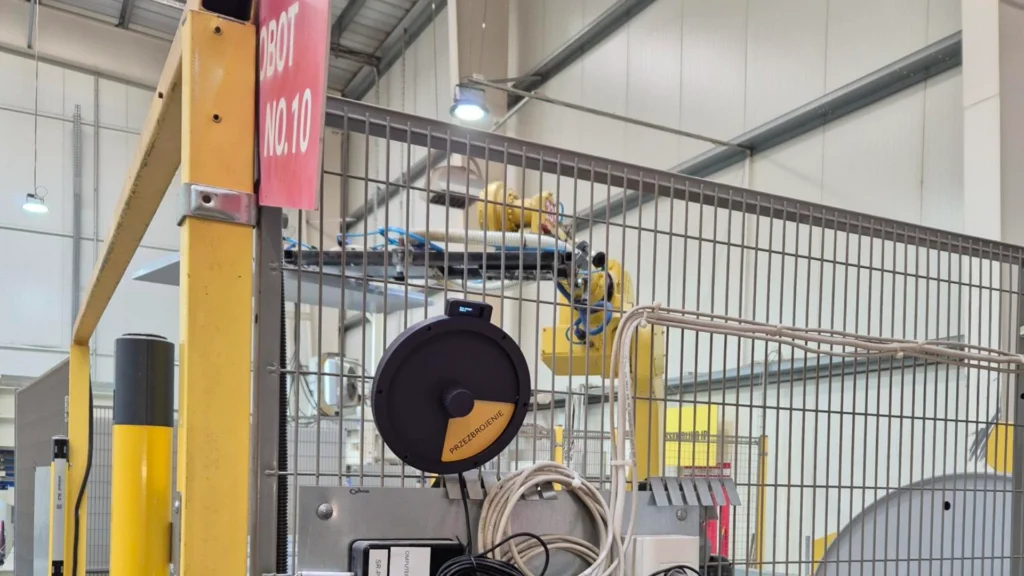
Autor: Piotr Wiśniewski
Zobacz więcej o IIoT i IoT DBR
Zobacz też wideo: