In today’s fast-paced manufacturing world, success depends on having immediate access to accurate, up-to-date information about your production processes. When you lack full visibility into what’s happening on the shop floor, delays, unplanned downtime, and declining performance quickly become the norm. That’s why real-time production monitoring has become a foundation of modern plant management-empowering leaders to make better decisions, faster, and with greater confidence.
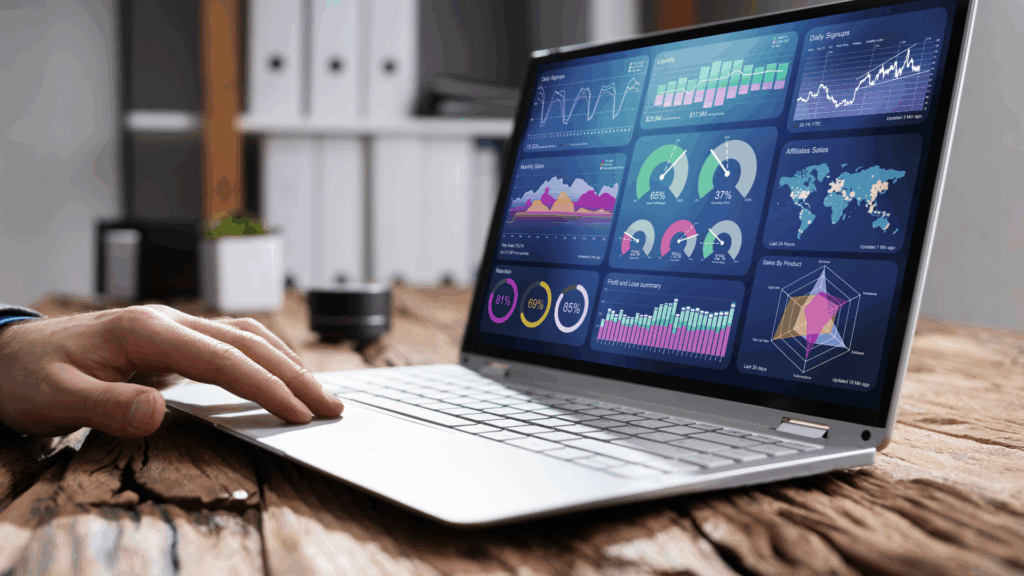
What Is Real-Time Production Monitoring?
Real-time production monitoring is the ongoing collection, transmission, and analysis of operational data from machines, production lines, and processes. This is achieved by installing IoT sensors on key equipment, which automatically feed data into analytics platforms and dashboards. As a result, managers and operators gain an up-to-the-minute, accurate picture of the shop floor-without the delays and errors of manual reporting. This transparency allows for immediate identification of issues and a proactive approach to problem-solving, rather than simply reacting to the consequences after the fact.
The Risks of Operating Without Real-Time Data
Operating without real-time data exposes companies to a range of hidden risks. For example, managers may only become aware of problems after they’ve already caused significant disruptions. Micro-downtime-those small, often unnoticed stoppages-can accumulate over time, quietly eroding efficiency and output. Without a clear view of production bottlenecks or the root causes of operational losses, it becomes nearly impossible to plan effectively or improve processes. Decisions are then made based on incomplete or outdated information, which can lead to missed targets, higher costs, and lost opportunities.
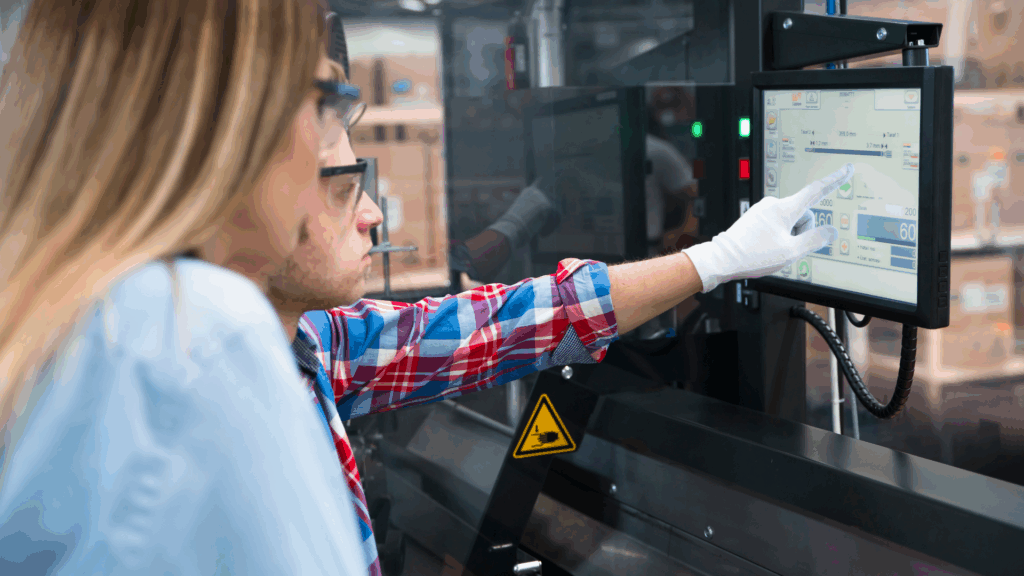
Why OEE Suffers Without Live Data
A key metric in manufacturing is Overall Equipment Effectiveness (OEE), which measures the combined impact of availability, performance, and quality. Without live data, the accuracy of OEE calculations drops significantly. This means you can’t quickly spot or react to declines in efficiency, and your planning is no longer grounded in the real operating conditions of your plant. As a result, you lose the ability to make timely adjustments that could prevent further losses or capitalize on improvement opportunities.
What Metrics Should You Track?
To truly understand and optimize your production, it’s important to monitor a comprehensive set of metrics, including:
- Machine uptime versus downtime, which highlights equipment reliability and utilization.
- The number of units produced compared to the production plan, helping you track progress and identify shortfalls.
- The number of defects and errors, which is essential for maintaining product quality.
- Key machine parameters such as temperature, pressure, and energy consumption, which can indicate emerging problems before they cause failures.
- Micro-downtime and cycle time, providing insight into hidden inefficiencies.
- OEE itself, combining availability, performance, and quality into a single, actionable metric.
By tracking these indicators in real time, you gain a holistic view of your operations and can respond proactively to emerging issues.
IoT in Action: Transforming the Shop Floor
Implementing IoT technologies is the most effective way to achieve real-time production monitoring. The process typically starts with installing sensors on critical machines and production lines. These sensors automatically transmit data to centralized analytics platforms, where it’s visualized on user-friendly dashboards. This setup allows you to see live results at a glance and quickly identify deviations from the norm.
Advanced systems, like those offered by DBR77, also incorporate AI algorithms that analyze operational data to detect anomalies and predict potential issues before they escalate. This means you can address problems before they lead to costly downtime or quality issues, further protecting your bottom line.
Real-World Results
The benefits of real-time production monitoring are not just theoretical-they’re proven in practice. For example:
- A Polish automotive plant saw a 20% increase in operational efficiency within just six months of implementing IoT monitoring on its assembly lines.
- A German furniture manufacturer reduced micro-downtime by 25% and improved the accuracy of production reporting by deploying digital sensors.
- An American logistics company cut warehouse equipment breakdowns by 30% through real-time monitoring of transport devices.
These examples demonstrate that real-time data leads directly to measurable improvements in efficiency, reliability, and quality.
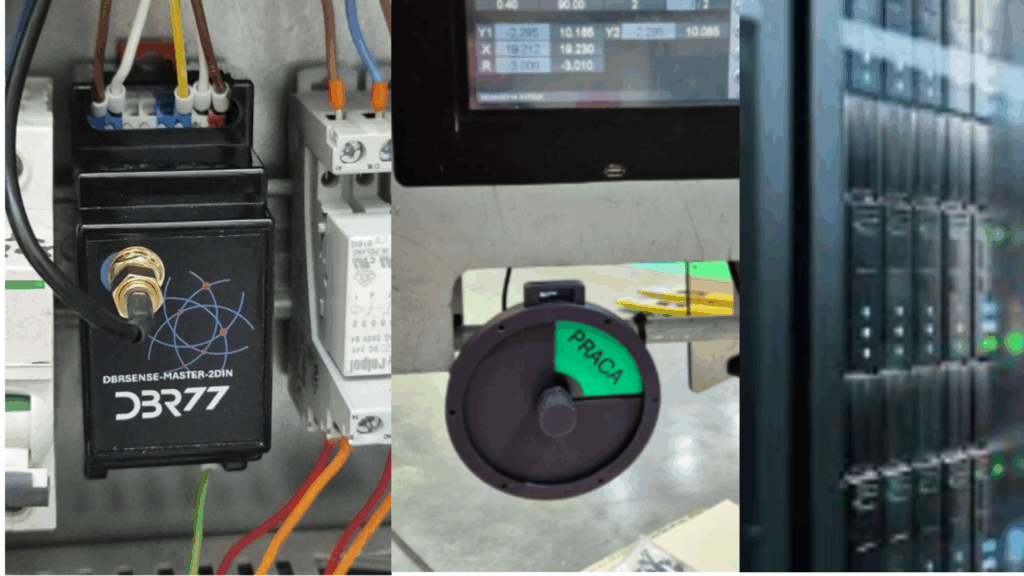
The Benefits of Fast Data Access
Having instant access to production data brings a wide range of advantages, including:
- The ability to respond immediately to problems, minimizing downtime and preventing minor issues from escalating.
- More precise planning of production and resource allocation, reducing waste and optimizing throughput.
- Faster, fact-based decision-making, allowing you to stay ahead of the competition.
- Better utilization of both human and technical resources, increasing overall productivity.
- Higher product quality, as deviations from standards can be detected and addressed in real time.
Best Practices for Implementation
To maximize the benefits of real-time monitoring, it’s important to follow proven best practices:
- Begin with your most critical machines or lines-those with the highest potential for improvement.
- Use sensors that collect only the data you truly need, avoiding information overload.
- Ensure data is visualized in clear, intuitive dashboards, so operators and managers can react quickly.
- Regularly analyze the data and adjust processes-not just collecting information, but using it to drive continuous improvement.
- Involve your team in the process; employee education and engagement are key to successful adoption and long-term results.
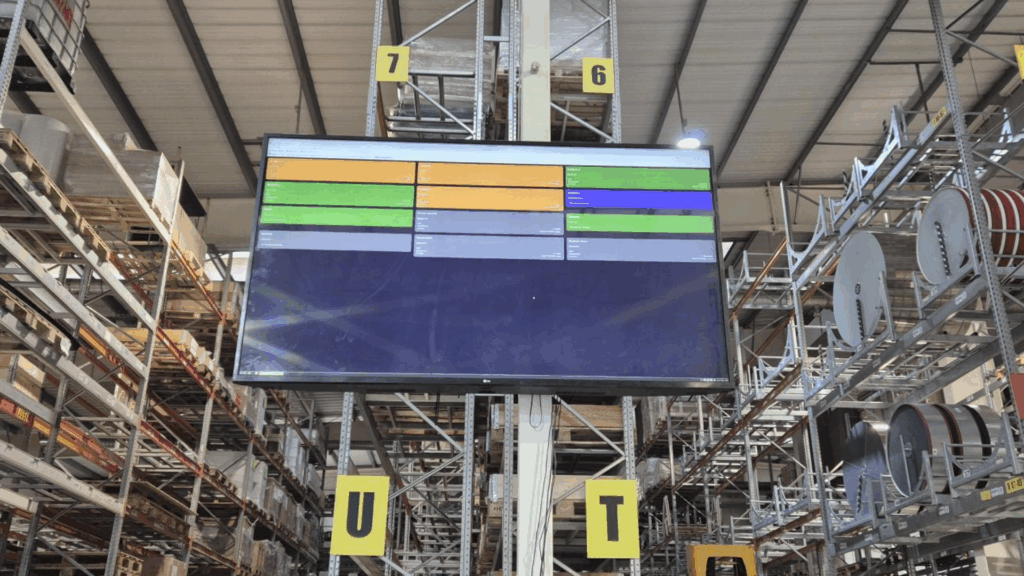
Why CEOs Choose DBR77 for IoT Production Monitoring
DBR77 provides a comprehensive, cloud-based IoT system designed for real-time data collection, analysis, and actionable insight. With its own sensors and advanced analytics platform, DBR77 enables seamless monitoring of all key production metrics. Data flows directly from machines to a digital twin of your production environment, allowing for real-time OEE monitoring, identification of micro-downtime and unplanned stoppages, and rapid root-cause analysis of efficiency drops.
The system is ready to use after a short implementation period and does not require costly IT infrastructure overhauls. This makes DBR77 an accessible and scalable solution for manufacturers of any size who want to boost efficiency and profitability through data-driven decision-making.
Ready to Transform Your Production?
Unlock the full potential of your manufacturing operations with DBR77’s IoT platform. Gain real-time visibility, reduce downtime, and make every decision data-driven.
Discover how IoT DBR77 can boost your efficiency and profitability-visit our IoT solutions page today!
Finally, we invite you to listen to our podcast, where we discuss the latest trends and practices in data-driven manufacturing. Subscribe to us on your favorite streaming platform so you don’t miss future episodes where we share inspiration, expert interviews and practical tips for production leaders.
Subscribe to stay up to date
https://factoryonair.buzzsprout.com
Book a free session with a DBR77 expert and see how our platform works in action.
Let’s talk: Book a meeting.
Until we hear from you!