This is another article in our series on IoT in manufacturing and its practical applications in industry. In previous texts, we discussed machine monitoring and production data analysis. Today we will focus on one of the key performance indicators – cycle time. How exactly do you measure it and how does the DBR77 IoT system help optimize it?
Purpose of the article
The purpose of this article is to present the DBR77 IoT sensor system as a way to automatically collect information on process cycle times and optimize them.
Definition and impact on operational efficiency
Cycle time is the time it takes to complete the full production process of one unit of a product at a given station. Its precise measurement makes it possible to identify losses, reduce inefficient operations and better synchronize the operation of machines. This allows companies to eliminate excessive downtime and improve the efficiency of the entire production process.
Influence on production planning and process optimization
Cycle time data are essential for effective production management. They allow better planning of schedules, minimizing losses due to unforeseen downtime and optimizing resource utilization. With DBR77’s IoT system, automatic data collection and analysis is possible. This makes it possible to make improvements in real time, increasing the competitiveness and operational efficiency of the company.
Fundamentals of sensor technology in manufacturing
The role of sensors in measurement automation
Today’s manufacturing plants rely on process automation, and one of the key elements in this transformation is sensors. They play an important role in monitoring production, enabling precise cycle time measurement without human intervention. This eliminates human error due to inaccuracy, fatigue or subjective judgment of operators.
Sensors enable real-time data collection, allowing quick analysis and response to any deviations from the norm. This information can be used not only to optimize individual operations, but also to implement predictive maintenance methods that help avoid machine failures and minimize downtime.
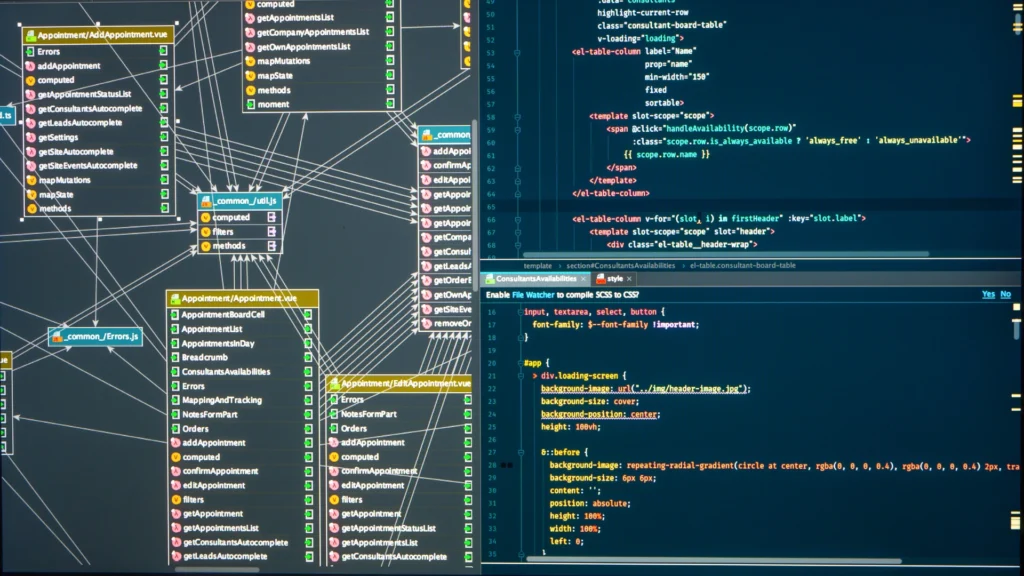
Integration of sensors with monitoring systems (IoT, MES, ERP, digital twin)
Today’s companies are increasingly using comprehensive production management systems that allow the integration of data from various sources. Sensors can be connected to systems such as:
- IoT (Internet of Things) – enables sensor data to be sent to central cloud databases and analyzed in real time. DBR77’s IoT system allows for comprehensive monitoring of production equipment and processes, providing key information on operational efficiency and enabling automatic response to changes in real time.
- MES (Manufacturing Execution System) – A production operations management system that helps monitor and optimize processes.
- ERP (Enterprise Resource Planning) – An enterprise resource management system that allows production data to be synchronized with other company departments, such as logistics and finance.
- Digital Twin – a virtual model of an actual manufacturing plant that allows testing various optimization scenarios without affecting the actual process. With the digital twin technology offered by DBR77’s IoT system, companies can accurately simulate changes in production processes and anticipate potential disruptions, allowing them to manage production even more efficiently.
By integrating sensors with these systems, it is possible to comprehensively monitor production, identify potential problems and implement preventive measures based on real data.
Methodology for determining cycle time
In order to effectively determine cycle time, it is crucial to identify a single event or activity that is repetitive during process execution and can be precisely measured. A sensor is installed at the location where it occurs, which automatically records when a particular stage of production begins and ends.
Example 1: Plastic injection molding process
In the case of injection molding machines, the cycle time can be determined by the operation of pulling the finished part from the mold. Since this process takes place in each production cycle, mounting a sensor on the robotic arm receiving the product makes it possible to determine precisely when one cycle ends and the next begins. The recorded data makes it possible to analyze the efficiency of the process, identify delays and assess the stability of the machine’s operation.
Example 2: Manual position
In a manual manufacturing process, where an operator pulls components from a container and assembles them into a final product, cycle times can be determined by monitoring when a new component is reached. An optical or proximity sensor mounted next to the container records each time a component is picked up, allowing for accurate determination of times between operations. Such measurement makes it possible to assess operator productivity, optimize station ergonomics and identify potential time losses.
By using this method, companies can better analyze their production processes, identify bottlenecks and make decisions to improve operational efficiency.
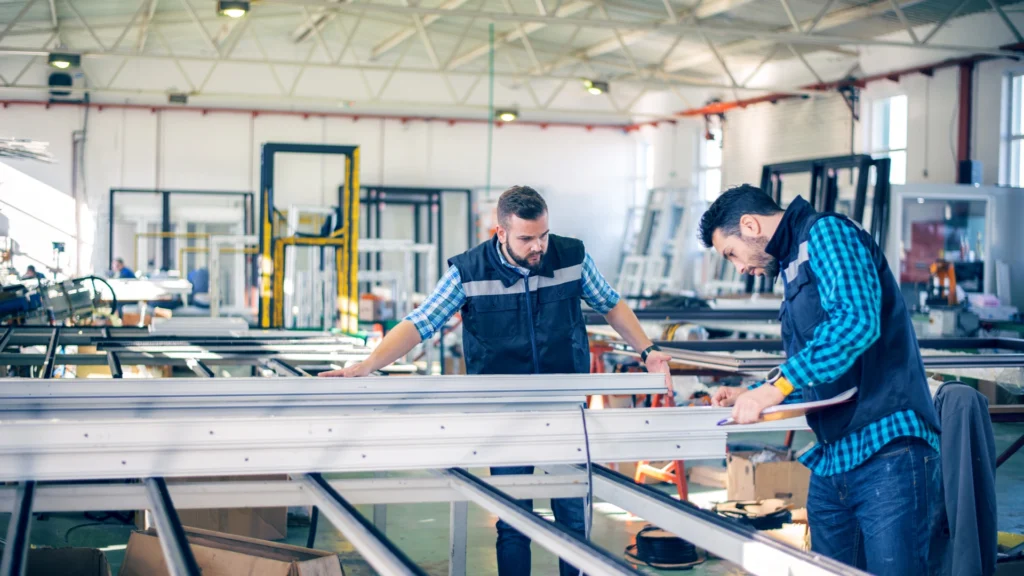
What are the benefits of this method?
The use of sensors to measure cycle time in manufacturing processes brings a number of important benefits. First and foremost, it allows for increased measurement accuracy, eliminating errors due to manual monitoring that can lead to inaccuracies in operational efficiency analysis. As a result, measurement automation provides precise, real-time data. The DBR77 system enables them to be intelligently analyzed and immediately used to optimize production. This translates into better process control.
In addition, this method reduces the number of sensors needed, as it is often sufficient to place a single sensor at a key point to obtain comprehensive cycle information. This reduces installation and maintenance costs while maintaining the high quality of the data collected.
The greatest value of this method, however, is the ability to analyze and optimize processes based on real data. Access to precise information through DBR77’s IoT system enables better production planning, identification and elimination of bottlenecks, and more effective management of operational efficiency. As a result, companies can increase their competitiveness, reduce downtime and use resources more efficiently.
Types of sensors and their application in the DBR77 system
System DBR77 uses a variety of sensors to monitor production processes. They make it possible to automate measurements, optimize operations and increase machine efficiency and reliability. Below are the key types of sensors used in the system and their importance in production management.
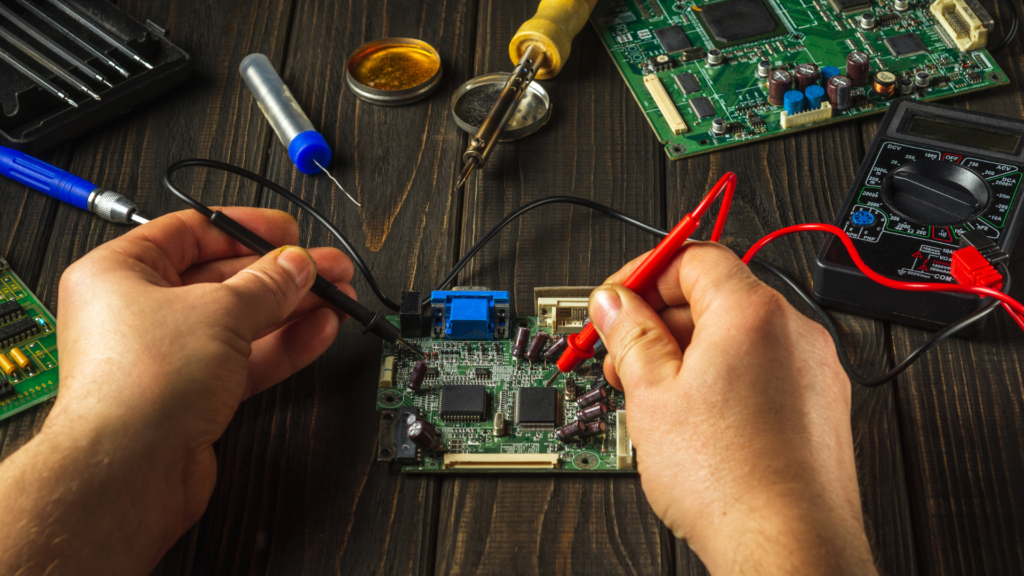
Proximity sensor
Proximity sensors allow detection of objects without physical contact. They operate on the principle of magnetic field, ultrasound, infrared or capacitive technology, which allows them to be used in a variety of industrial settings. Magnetic sensors detect only metallic components, while capacitive sensors can also register non-conductive materials such as plastics. Ultrasonic and infrared versions work well for measuring distances, making it possible to determine the exact position of objects.
In the system DBR77 Proximity sensors are used in automating assembly processes. Also, in detecting components on production belts and protecting machines from collisions. Thanks to them, the system can dynamically respond to changes in the layout of the production line, which minimizes the risk of errors and downtime. They are also used in vision systems for product identification, which improves sorting and quality control.
Barrier sensor
Barrier sensors work on the principle of a light beam transmitted between a transmitter and a receiver. When the beam is interrupted by an object, the system immediately registers the event. This makes it possible to accurately detect the movement and presence of products on the production line. By using infrared or lasers, these sensors can operate with high accuracy, even in harsh environmental conditions such as high dust or intense lighting.
In the system DBR77 Barrier sensors are used to control product flow on assembly and sorting lines. They enable machines to automatically stop and start depending on the presence of an object, improving safety and optimizing operation. In addition, they have a protective function – if motion is detected in the danger zone, they can immediately shut down the machine, preventing potential accidents.
Vibration sensor
Vibration sensors monitor vibrations of industrial machinery and structures, recording their intensity and frequency. They work by measuring the dynamic forces that result from the rotational and linear motion of mechanical components. They use piezoelectric technology or accelerometers to detect changes in the normal operation of equipment, allowing rapid diagnosis of problems.
In the systemDBR77 Vibration sensors play a key role in predictive maintenance of machinery. By analyzing changes in vibration characteristics, the system is able to detect early signs of wear on mechanical components such as bearings or drive shafts. This makes it possible to plan repairs in advance and minimize unplanned downtime, significantly increasing the operational efficiency of manufacturing plants.
Energy meters
Energy meters are used to monitor the power consumption of industrial machinery and equipment. They work by recording key parameters such as voltage, current, power consumption and power factor. The data is collected in real time and sent to a central analysis system. They are then used to identify areas of high energy consumption and optimize machine operation.
In the system DBR77 Energy meters play an important role in managing the energy efficiency of a plant. They make it possible to identify inefficient processes and implement measures to reduce energy losses. Real-time monitoring of energy consumption also enables rapid response to sudden changes in power consumption. This helps prevent overloads and optimize operating costs.
Operator declaration button
The operator declaration button is a manual interface that allows workers to record important events in the production system. It can be connected to an MES or HMI system, allowing information to be sent immediately to a central database. This allows operators to report the start and end of machine operation, causes of downtime and other significant events affecting production.
In the system DBR77 The operator declaration button plays a key function in analyzing working time and optimizing production schedules. By manually recording work statuses, it is possible to accurately determine the impact of human factors on production line downtime and productivity. This information is used to improve work organization and implement improvements that eliminate unnecessary interruptions and improve operational efficiency.
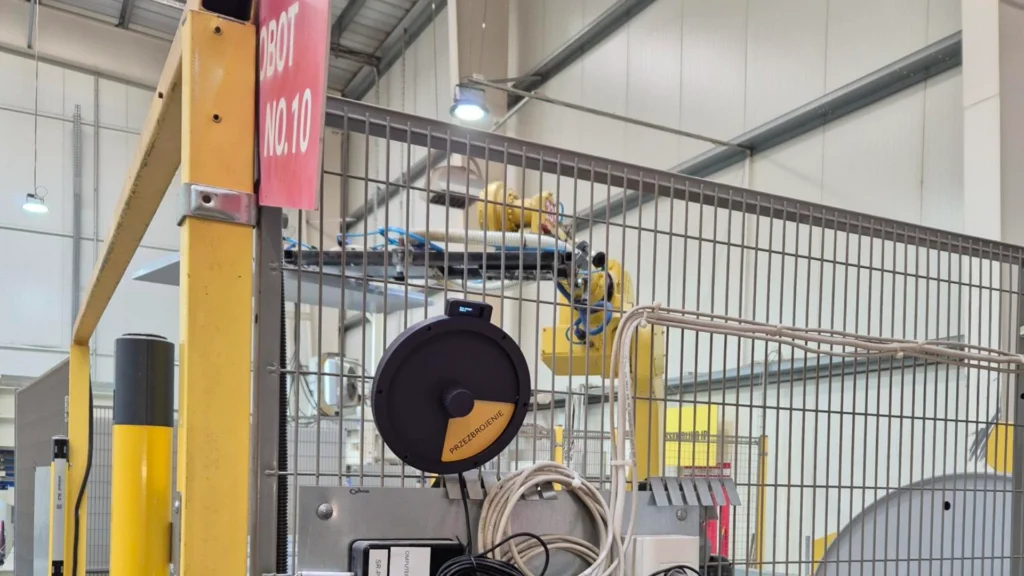
Autor: Piotr Wiśniewski
See also video: