Defective products generate not only direct financial losses but also damage a company’s reputation and lead to customer churn. In today’s competitive market, quality is more than just a final check-it’s a continuous process supported by technology at every stage. In this post, we’ll explore how modern solutions like vision systems, IoT, and data analytics can significantly improve production quality. We’ll also show how DBR77 supports quality control through automated production data analysis.
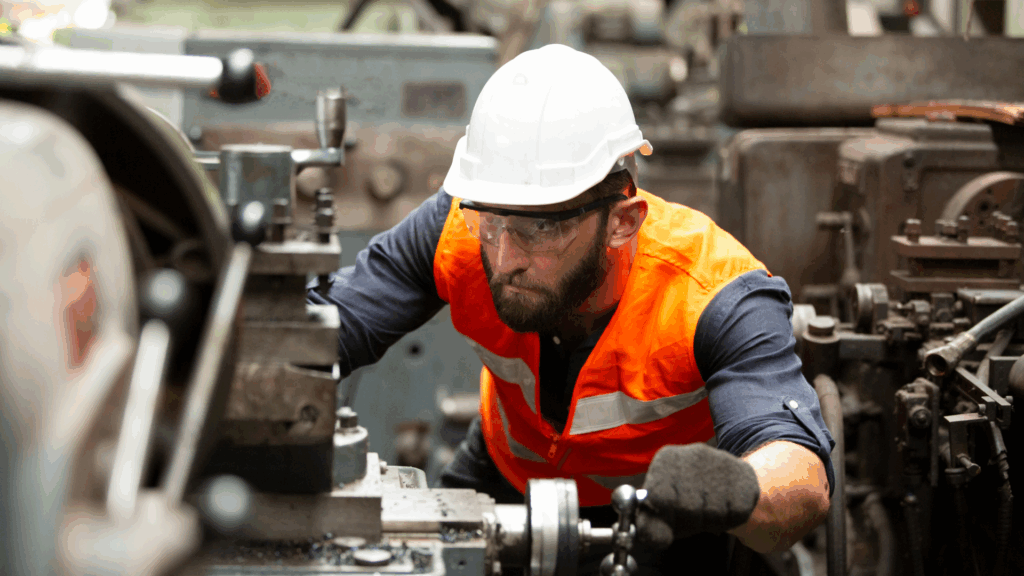
The Impact of Defective Products
Poor quality products have far-reaching consequences. Direct costs include returns, complaints, and the need for rework. Indirect costs are often even more damaging: loss of customer trust, brand image erosion, and the expense of recertifying products. Over time, these issues can reduce market share, make it harder to win new business, and increase sales and marketing costs. Defects also negatively affect the morale of production teams and quality controllers, making quality improvement a company-wide priority.
How Vision Systems Detect Defects
Vision systems combine cameras, lighting, and real-time image analysis software to inspect products as they move through production. These systems can detect surface defects like cracks, scratches, or deformations, assembly errors, dimensional deviations, and incorrect colors, labels, or markings. The speed and precision of vision systems make it possible to identify flaws that would be missed by manual inspection, ensuring that only products meeting specifications reach the customer.
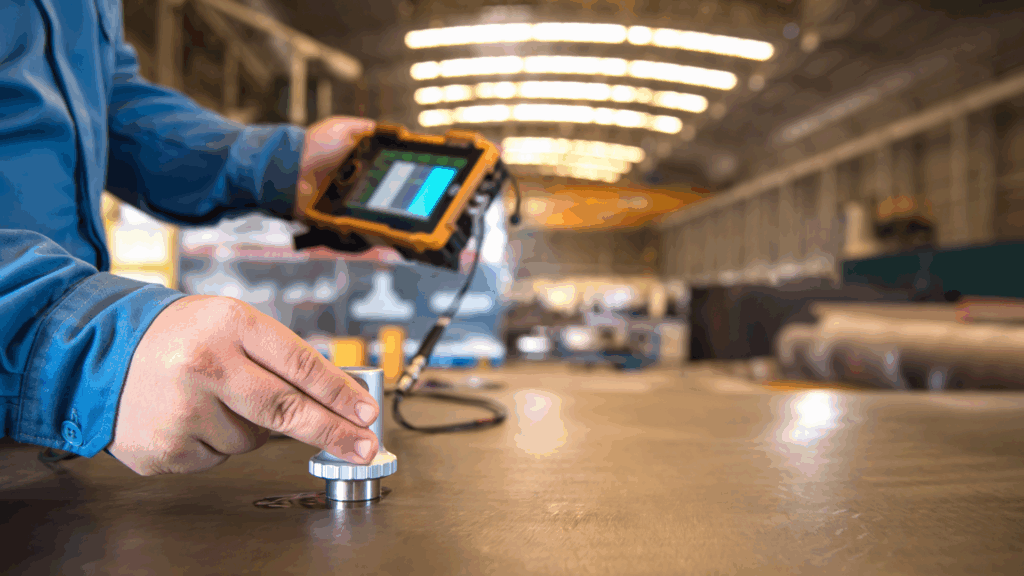
The Importance of Monitoring Production Conditions
Production conditions-temperature, humidity, pressure, and vibration-have a significant impact on final product quality. Real-time monitoring of these parameters helps maintain optimal process conditions and can provide early warning of potential issues before defects appear. Even small fluctuations can signal problems that, if left unchecked, may result in costly quality failures down the line.
Real-World Examples of Quality Improvement
- An electronics factory reduced customer complaints by 45% after implementing vision systems for defect detection.
- A PET bottle manufacturer lowered its defect rate by 30% by monitoring forming temperatures more closely.
- An automotive plant cut warranty costs by 20% in a single year through the combined use of vision inspection and environmental monitoring.
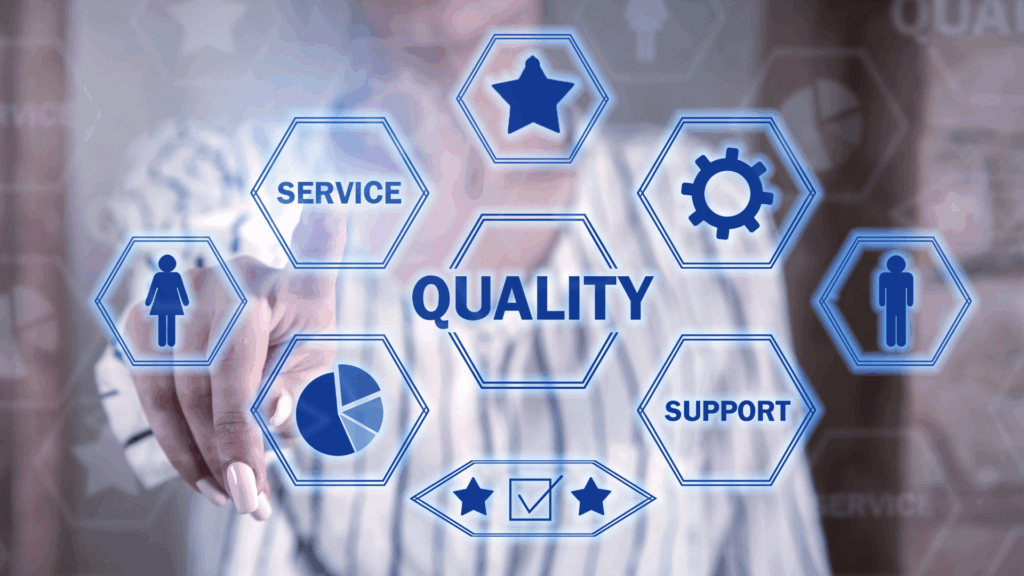
How DBR77 Supports Quality Control
DBR77 collects data from machines, production lines, and vision systems in real time. Combined with a digital twin of the plant, this enables simulation of how changes in production conditions impact product quality. The platform automatically analyzes quality trends and detects deviations from standards as soon as they arise. With the DBR77 AI Assistant, users receive recommendations for process optimization before serious quality issues develop.
Benefits of Automated Data Analysis
Automated data analysis enables early detection of trends that could lead to quality drops, reducing the number of defects without increasing the size of the quality control team. Real-time alerts allow for immediate response to issues, while continuous monitoring eliminates delays and subjective assessments. This approach ensures that quality remains consistently high, batch after batch.
Challenges in Implementing Quality Control Systems
Deploying advanced quality control systems comes with its own set of challenges. Vision systems must be calibrated and tailored to the specific product. Integration with existing production and ERP systems is essential for seamless operation. There’s also a cultural shift required-from end-of-line inspection to in-process quality control-and investment in the right technical infrastructure, including sensors, cameras, and data servers.
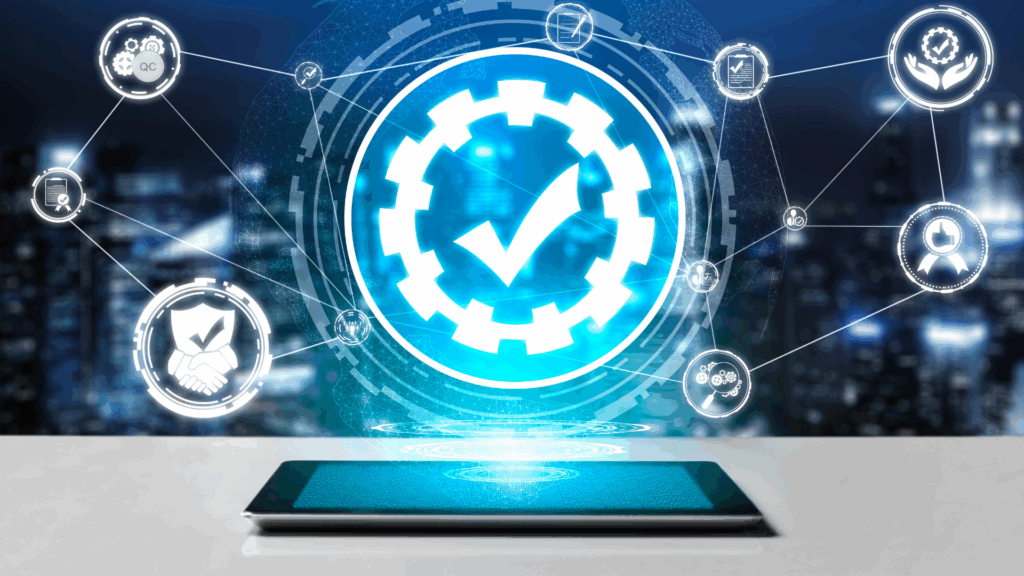
Practical Steps to Improve Quality
- Analyze the root causes of current defects and complaints.
- Identify critical points in the production process where quality risks are highest.
- Implement real-time monitoring of production conditions.
- Deploy vision systems at key stages of production.
- Collect and analyze production data continuously.
- Train production and quality teams on new tools and procedures.
- Continuously optimize process parameters based on data insights.
The Impact on Customer Satisfaction
Higher product quality means fewer complaints and greater customer loyalty. Strong quality performance enhances your company’s credibility with new customers and business partners. Ultimately, improving quality strengthens your brand and builds a lasting competitive advantage in the market.
Ready to take your quality control to the next level?
Discover how DBR77’s integrated platform and AI-powered analytics can help you reduce defects, improve customer satisfaction, and build a reputation for excellence. Visit our IoT DBR77 solutions page to learn more.
Finally, we invite you to listen to our podcast, where we discuss the latest trends and practices in data-driven manufacturing. Subscribe to us on your favorite streaming platform so you don’t miss future episodes where we share inspiration, expert interviews and practical tips for production leaders.
Subscribe to stay up to date
https://factoryonair.buzzsprout.com
Book a free session with a DBR77 expert and see how our platform works in action.
Let’s talk: Book a meeting
Until we hear from you!