High operational costs-energy, materials, and labor-are among the biggest barriers to improving profitability in manufacturing. Many companies struggle to maintain margins as expenses rise, but with the right data and tools, it’s possible to cut costs and use resources more efficiently. In this post, we’ll explore how data analysis and process simulation help lower costs and boost efficiency, and how DBR77 supports energy and material optimization at every step.
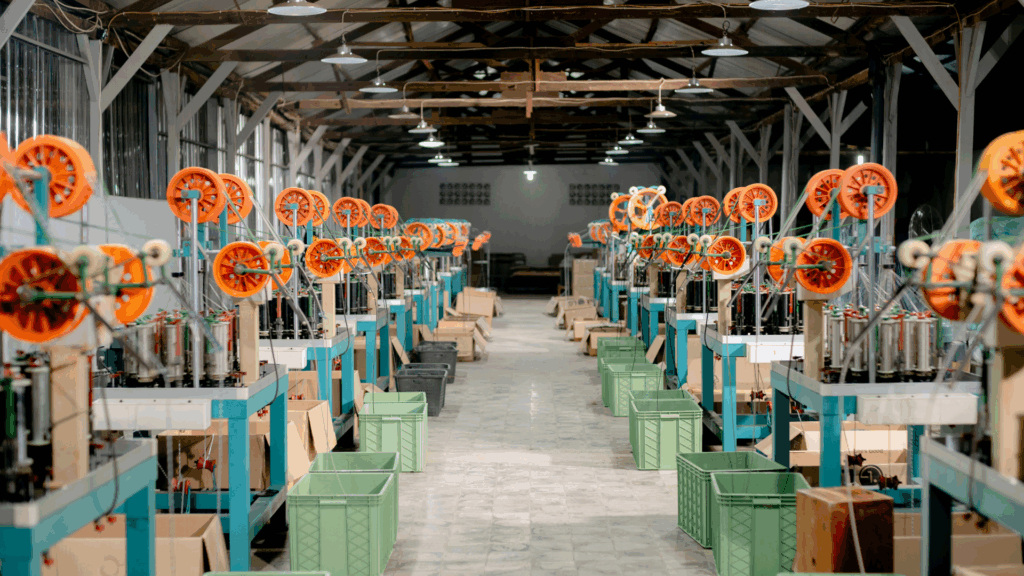
Main Sources of High Costs in Manufacturing
Operational costs can escalate for several reasons:
- Energy consumption: Inefficient machines, unnecessary idling, and lack of optimization during peak hours all drive up energy bills.
- Material losses: Overproduction, production errors, and poor raw material storage lead to waste and higher expenses.
- Inefficient processes: Suboptimal workflows, long cycle times, and frequent downtime reduce productivity.
- Labor costs: Paying for time lost to inefficient organization and waiting increases wage expenses.
- Unplanned repairs and breakdowns: Without predictive maintenance, emergency service and downtime become more frequent and costly.
How to Monitor Energy Consumption in Real Time
Reducing energy costs starts with visibility. By installing IoT sensors on critical machines and production lines, you can continuously monitor energy usage across different work cycles. Real-time alerts notify you when consumption exceeds set thresholds, and trend analysis highlights areas with the greatest savings potential. Comparing energy use with actual production output helps identify inefficiencies and guides targeted improvements.
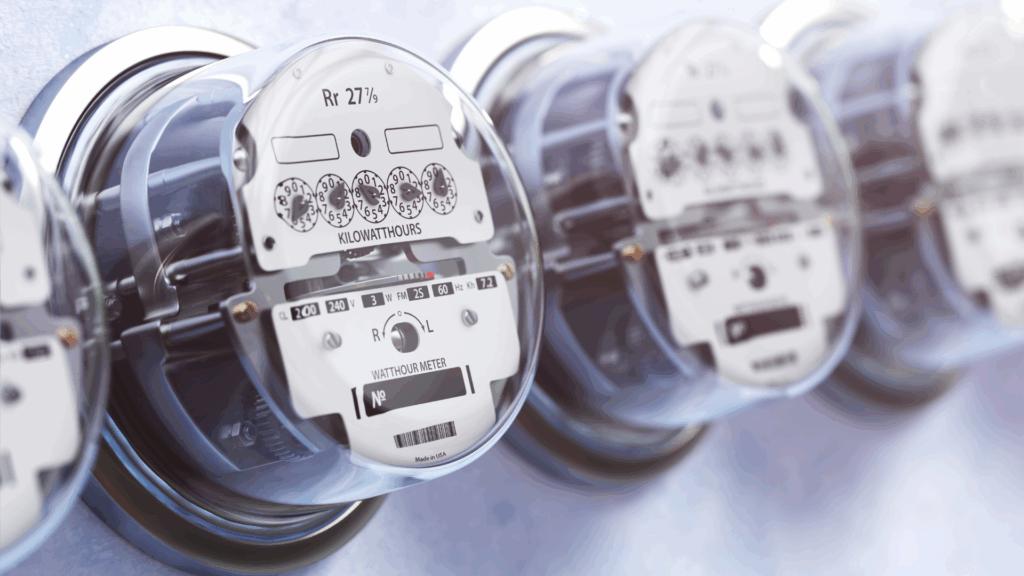
The Role of Simulation in Planning Savings
Simulations let you test different operating scenarios in a virtual environment-without risking real-world losses. For example, you can see how changing the order of machine operations affects energy use, how reorganizing logistics impacts fuel consumption for transport vehicles, or how different maintenance strategies influence service costs. Simulations help select the most economical scenarios before making changes on the shop floor.
Real-World Examples of Cost Reduction
- A chemical plant reduced energy use by 15% after optimizing machine operating schedules.
- A food manufacturer cut material waste by 20% through data-driven production analysis and reduced overproduction.
- A logistics company lowered internal transport costs by 18% by optimizing routes and warehouse operations.
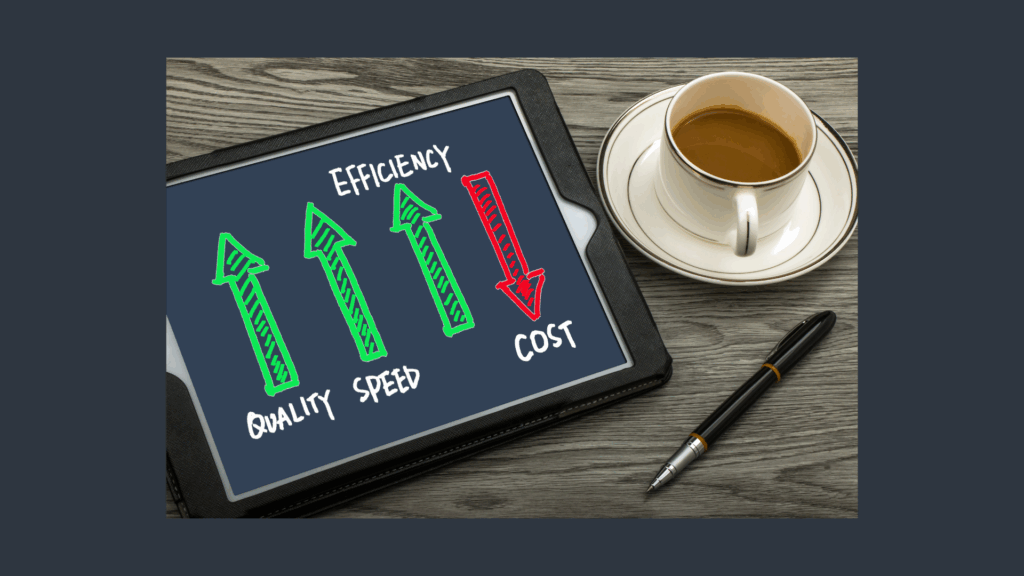
How DBR77 Supports Resource Optimization
DBR77 collects real-time operational data from machines, production lines, and logistics systems. With a digital twin of your facility, you can simulate the impact of changes on energy and resource consumption before implementing them. The platform analyzes resource usage relative to actual production performance, and AI algorithms recommend cost-saving actions-like adjusting machine schedules or reorganizing workflows for greater efficiency.
Benefits of Integrated Cost Data
Bringing all cost data into a single analytics platform provides a complete, real-time view of operational spending. By connecting production, energy, material, and labor data, you can generate precise cost reports for both operations and finance teams. This level of insight enables better investment decisions, based on the real impact of costs on profitability.
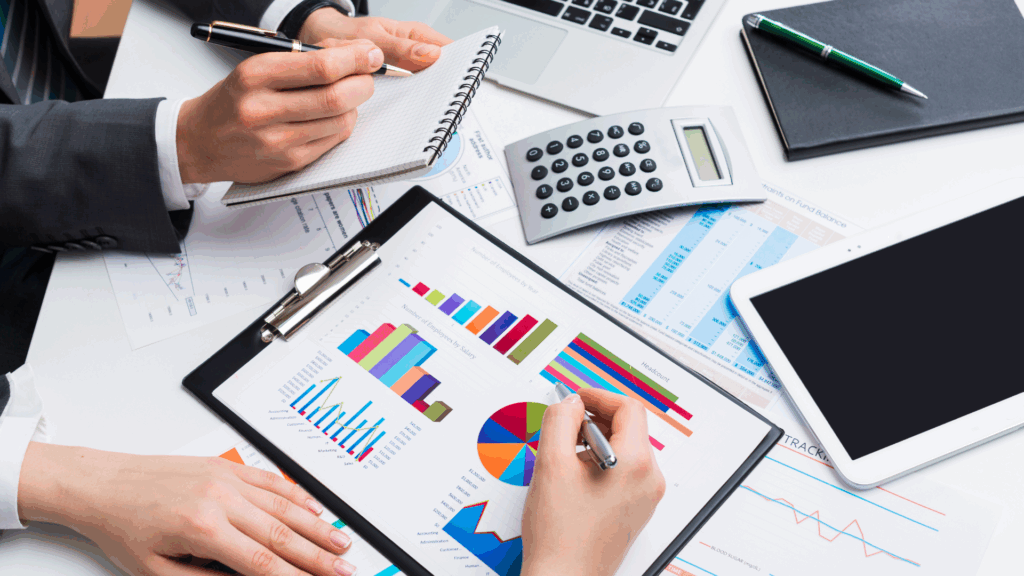
Challenges in Changing Operational Habits
Shifting to a data-driven, cost-optimized approach isn’t always easy. Employees may resist changes to established routines, and updating procedures or standards can cause short-term dips in productivity. Integrating new tools with existing ERP or MES systems takes planning, and ongoing monitoring is needed to ensure optimization efforts stay on track.
Practical Steps to Reduce Costs
- Audit current energy and material usage to establish a baseline.
- Identify the biggest sources of waste and inefficiency.
- Implement real-time monitoring to track usage.
- Simulate alternative workflows and organizational scenarios.
- Train employees on cost optimization best practices.
- Review and update savings strategies regularly to sustain improvements.
The Impact of Savings on Competitiveness
Lowering operational costs directly increases margins and improves profitability. It enables you to offer more competitive pricing without sacrificing quality, and makes your business more resilient to fluctuations in raw material or energy prices. Savings also free up capital for investment in growth and new technologies, strengthening your position in both local and global markets.
Ready to make your operations more efficient and profitable?
Discover how DBR77’s data-driven platform and digital twin technology can help you monitor costs, simulate improvements, and unlock real savings. Visit our IoT DBR77 solutions page to learn more.
Finally, we invite you to listen to our podcast, where we discuss the latest trends and practices in data-driven manufacturing. Subscribe to us on your favorite streaming platform so you don’t miss future episodes where we share inspiration, expert interviews and practical tips for production leaders.
Subscribe to stay up to date
https://factoryonair.buzzsprout.com
Book a free session with a DBR77 expert and see how our platform works in action.
Let’s talk: Book a meeting
Until we hear from you!