Czyli jak mierzyć i optymalizować automatycznie czas cyklu?
Czym jest czas cyklu i dlaczego jest ważny w produkcji?
Czas cyklu to czas potrzebny na wykonanie pełnego procesu produkcyjnego jednej jednostki produktu na danym stanowisku, obejmujący zarówno operacje robocze, jak i niezbędne przerwy czy przestoje. Jego pomiar pozwala na lepszą kontrolę nad wydajnością operacyjną, a także na identyfikację potencjalnych obszarów do optymalizacji.
W kontekście zarządzania produkcją, czas cyklu odgrywa fundamentalną rolę w planowaniu procesów, eliminacji strat oraz poprawie efektywności operacyjnej. Dlatego krótszy czas cyklu oznacza większą zdolność produkcyjną, lepsze wykorzystanie zasobów i możliwość szybszej reakcji na zmieniające się warunki rynkowe.
Przykłady zastosowań czasu cyklu w różnych branżach
Czas cyklu ma zastosowanie w wielu gałęziach przemysłu. Na przykład w branży motoryzacyjnej precyzyjne określenie czasu cyklu na linii montażowej pozwala na synchronizację procesów i eliminację przestojów. Natomiast w produkcji elektronicznej mierzenie czasu cyklu umożliwia optymalizację pracy robotów i systemów montażowych, a w przemyśle spożywczym – zapewnia stabilność procesów pakowania i logistyki.
Z drugiej strony, w logistyce i magazynowaniu czas cyklu wykorzystywany jest do optymalizacji operacji kompletacji zamówień, gdzie krótszy czas realizacji przekłada się na wyższą satysfakcję klienta. Odpowiednio w usługach, takich jak centra obsługi klienta, analiza czasu cyklu pozwala na poprawę szybkości i jakości obsługi.
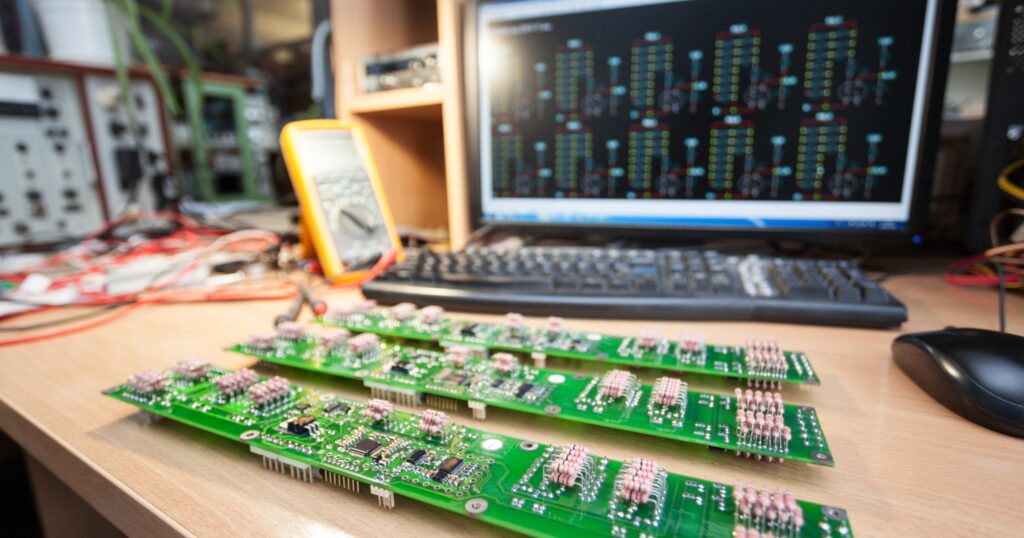
Powiązanie czasu cyklu z efektywnością operacyjną
Efektywność operacyjna to jeden z głównych celów optymalizacji procesów produkcyjnych. Czas cyklu jest bezpośrednio związany z wskaźnikami, takimi jak OEE (Overall Equipment Effectiveness) oraz takt czas, które pomagają określić, jak efektywnie wykorzystywane są dostępne zasoby.
Zrozumienie i optymalizacja czasu cyklu pozwala firmom minimalizować straty wynikające z przestojów, nadmiernej produkcji czy nieefektywnego wykorzystania mocy przerobowych, dzięki temu przedsiębiorstwa mogą lepiej dostosować się do zmieniających się warunków rynkowych, zwiększyć swoją konkurencyjność i osiągać wyższą rentowność.
Metody pomiaru czasu cyklu
Cykle produkcyjne możemy mierzyć ręcznie bądź automatycznie. Ręczne mierzenie czasu cyklu to jedna z najprostszych, ale jednocześnie najbardziej podatnych na błędy metod. Polega na fizycznej obserwacji procesu i rejestrowaniu czasu trwania poszczególnych operacji przy użyciu stopera lub innych narzędzi manualnych.
Zalety i wady podejścia manualnego
Zalety:
- Niski koszt wdrożenia – nie wymaga zaawansowanej technologii.
- Możliwość szybkiej analizy i reakcji na bieżące problemy.
- Łatwe do zastosowania w małych zakładach produkcyjnych.
Wady:
- Duża podatność na błędy ludzkie.
- Wysoki koszt pozyskanych informacji.
- Ograniczona możliwość ciągłego monitoringu.
Współczesna technologia pozwala na automatyzację pomiaru czasu cyklu za pomocą systemów IoT oraz inteligentnych czujników. Automatyczne rozwiązania eliminują błędy ludzkie i zapewniają precyzyjne dane w czasie rzeczywistym.
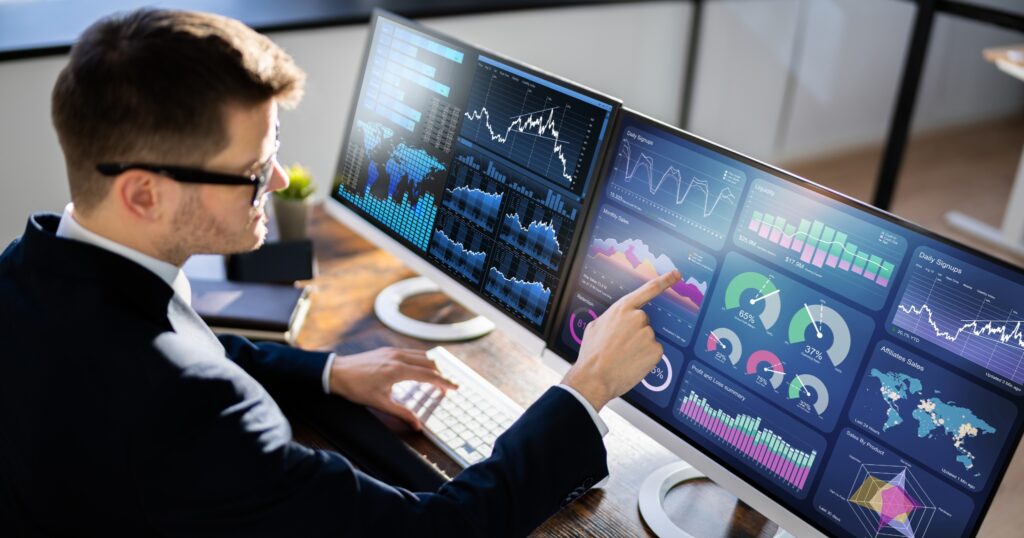
Zalety automatycznego pomiaru:
- Pełna eliminacja błędów ludzkich.
- Ciągły monitoring bez konieczności angażowania operatorów.
- Dostęp do precyzyjnych danych w czasie rzeczywistym.
- Możliwość natychmiastowej analizy i optymalizacji procesów.
Przykłady rozwiązań automatycznych
Przykłady zastosowań:
- Linie montażowe – monitorowanie czasu trwania każdej operacji na stanowiskach roboczych.
- Maszyny CNC – precyzyjne pomiary czasu obróbki i wykrywanie nieplanowanych przestojów.
- Przenośniki taśmowe – analiza przepływu materiałów i czasu transportu wewnętrznego.
- Systemy pakowania – optymalizacja cyklu operacji pakujących.
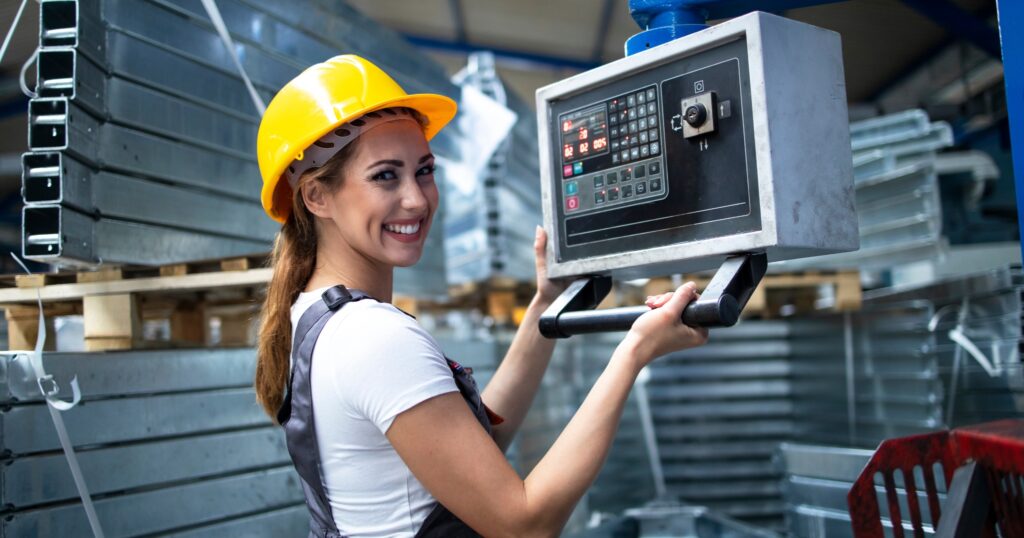
Wykorzystanie czasu cyklu do wyznaczenia standardu operacji
Standard operacji to określona, powtarzalna procedura wykonania danego procesu w określonym czasie. Dzięki temu definiowanie standardu pozwala na zwiększenie wydajności, redukcję strat oraz lepszą kontrolę nad jakością produkcji. Ponadto, wdrożenie jasno określonych standardów pozwala na minimalizację nieefektywności i poprawę przewidywalności operacji.
Analiza czasu cyklu pozwala na określenie realnego normatywnego czasu operacji. Proces ten obejmuje:
- Pomiar rzeczywistych czasów cyklu dla poszczególnych etapów produkcji.
- Identyfikację i eliminację anomalii oraz strat czasowych.
- Wyznaczenie wartości średniej i określenie optymalnego zakresu czasowego dla danej operacji.
- Zastosowanie normatywnego czasu operacji jako punktu odniesienia do dalszej optymalizacji.
Rola standardu w optymalizacji i planowaniu procesów
Dlaczego standaryzacja jest kluczowa dla efektywności
Standaryzacja operacji pozwala na osiągnięcie powtarzalnych wyników, zwiększenie produktywności i redukcję marnotrawstwa. Dzięki precyzyjnemu określeniu normatywnych czasów operacji możliwe jest wyeliminowanie zbędnych działań i optymalizacja przepływu pracy.
Eliminacja strat i redukcja zmienności w procesach
Jednocześnie, główne źródła strat, takie jak przestoje, nadprodukcja czy błędy jakościowe, mogą być skutecznie eliminowane dzięki wdrożeniu standardów operacyjnych. Ponadto, redukcja zmienności w procesach pozwala na bardziej przewidywalne wyniki i zwiększenie stabilności operacyjnej.
Użycie standardów do planowania zdolności produkcyjnych i optymalizacji kosztów
Znajomość normatywnych czasów operacji pozwala na:
- Precyzyjne określenie zdolności produkcyjnych – planowanie liczby zasobów potrzebnych do realizacji zamówień.
- Redukcję kosztów – eliminacja nadmiernych zapasów i minimalizacja strat materiałowych.
- Lepsze zarządzanie personelem – optymalne przypisanie pracowników do stanowisk w oparciu o rzeczywiste zapotrzebowanie.
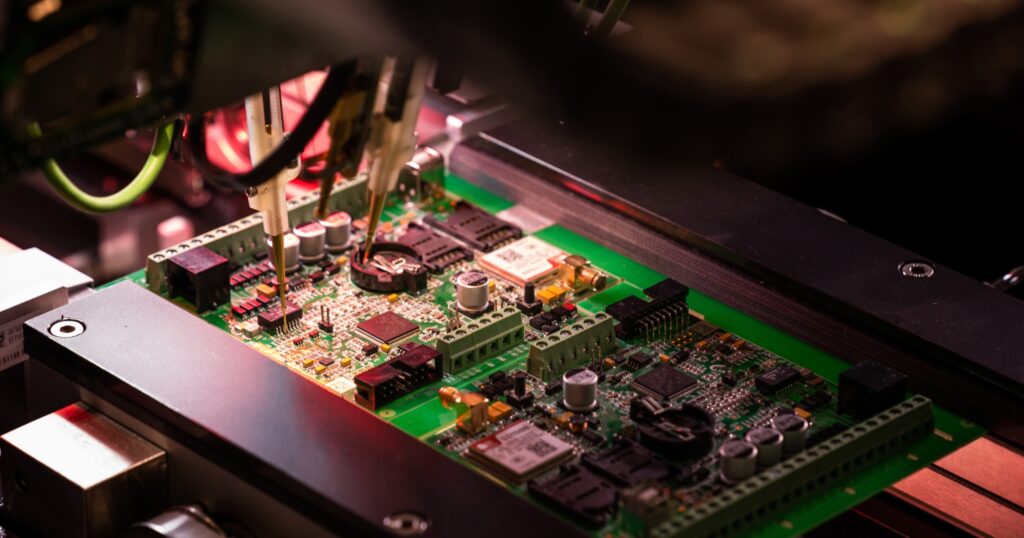
Rekomendacje dotyczące implementacji systemów automatycznego pomiaru
Dlatego, aby skutecznie wdrożyć systemy automatycznego monitorowania czasu cyklu, warto przestrzegać kilku kluczowych zasad:
- Dobór odpowiednich technologii – wybór czujników i systemów IoT dostosowanych do specyfiki procesu produkcyjnego.
- Integracja z istniejącymi systemami – połączenie systemu pomiarowego z ERP, MES i innymi narzędziami zarządzania produkcją.
- Analiza i interpretacja danych – wykorzystanie zaawansowanych algorytmów analizy danych do identyfikacji wzorców i optymalizacji operacji.
- Ciągłe doskonalenie – regularna aktualizacja standardów operacyjnych w oparciu o zebrane dane.
- Szkolenie personelu – zapewnienie pracownikom odpowiednich kompetencji do korzystania z systemów monitorowania.
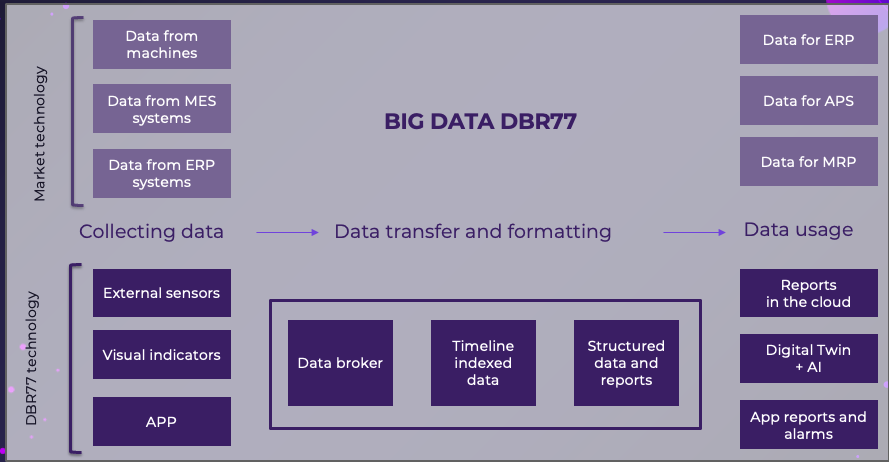
Podsumowanie i wnioski
Kluczowe korzyści wynikające z monitorowania czasu cyklu
Precyzyjny pomiar czasu cyklu przynosi znaczące korzyści dla przedsiębiorstw produkcyjnych. Umożliwia on:
Lepsze planowanie produkcji – bardziej precyzyjne harmonogramowanie i prognozowanie.
Zwiększenie efektywności – eliminacja strat wynikających z nieoptymalnych procesów i przestojów.
Poprawę zarządzania zasobami – lepsze wykorzystanie ludzi, maszyn i materiałów.
Identyfikację obszarów do optymalizacji – możliwość wprowadzenia usprawnień w organizacji pracy.
Redukcję kosztów operacyjnych – minimalizacja zużycia surowców, energii i czasu pracy.
Autor: Piotr Wiśniewski
Zobacz więcej o IoT DBR
Zobacz też wideo: