Kolejna odsłona case study wprowadzi Was w zagadnienie optymalizacji procesu pobierania materiału z magazynu do wydania na produkcję. Bliźniak Cyfrowy DBR77 pomógł producentowi z branży HVAC poradzić sobie z dużą zmiennością realizowanych produktów, a tym samym wybrać optymalne pobranie materiału z magazynu.
Opis przypadku
Nasz klient to producent urządzeń wentylacyjnych i chłodniczych. Zakład produkujący mieści się w województwie mazowieckim, zatrudniając ponad 150 osób pracujących na dwie zmiany produkcyjne. Jednak temat dotyczył obszaru magazynu, a konkretniej „pikowania”. Produkowane urządzenia są bardzo mocno customizowane, co zdecydowanie komplikuje kwestię pobrań. Ponadto, jeżeli uwzględnimy do tego średnią ilość pobrań na poziomie 800 elementów na zmianę to sytuacja robi się skomplikowana. Zakład ten mieści się w centralnej Polsce, pracuje na 2 zmiany i w obszarze analizy (magazyn – pick) pracuje łącznie 10 osób.

Opis zadania – pobranie materiału z magazynu
Wyzwanie klienta wynika z profilu produkowanych wyrobów. Na pierwszy rzut oka wyroby mogą wyglądać podobnie, ale mogą być one dopasowane do potrzeb klienta finalnego w szerokim zakresie. Kluczem do rozwiązania tego problemu było stworzenie możliwości generowania listy pobrań w dynamiczny sposób uwzględniający mix produktowy, który jest zaplanowany na dany dzień. Klient skorzystał z symulacji pobrań magazynowych w środowisku Bliźniaka Cyfrowego.
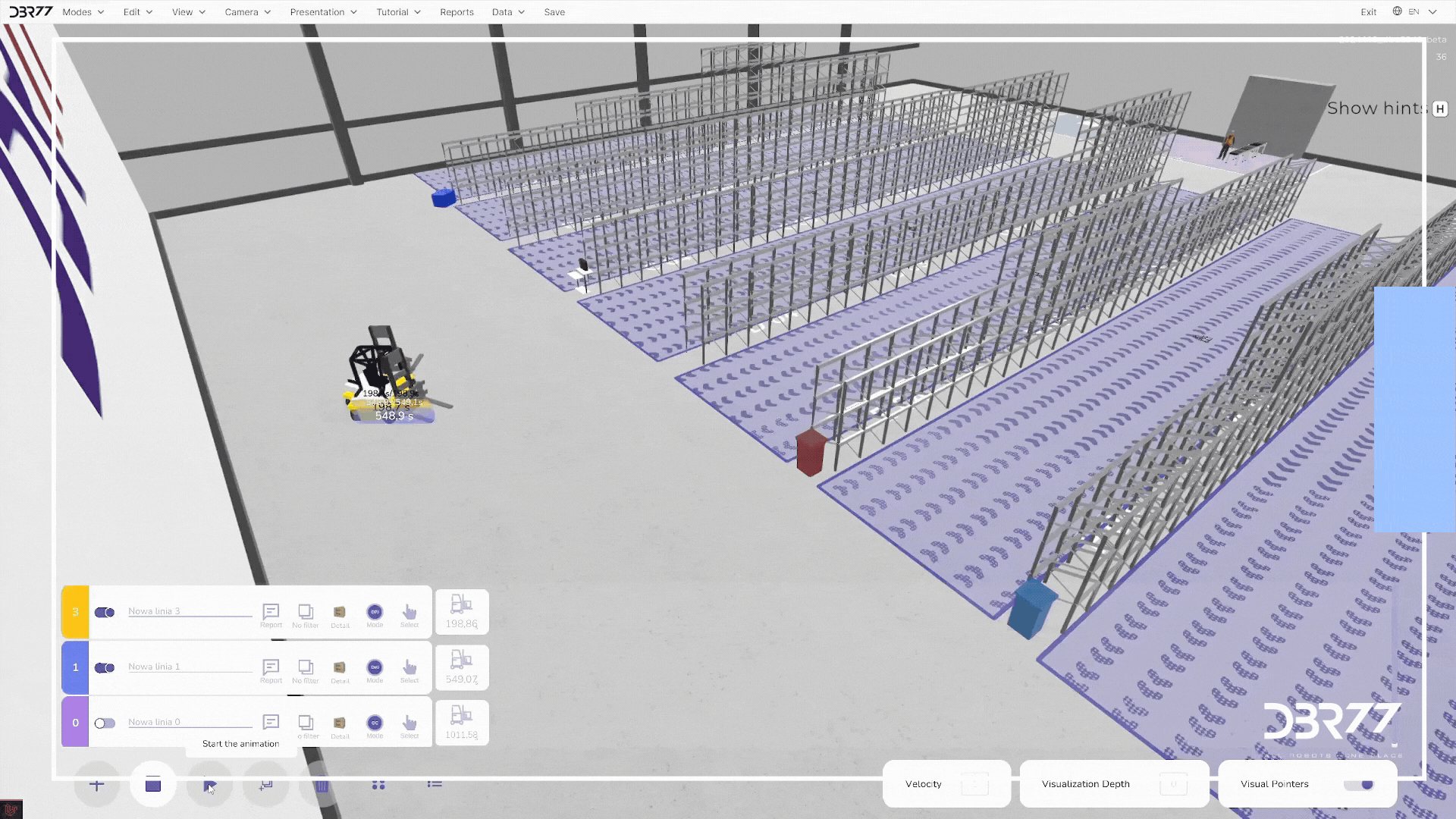
Zrealizowane prace
1. Budowa Bliźniaka Cyfrowego:
- Stworzenie bliźniaka cyfrowego odwzorowującego część magazynową.
- Opracowanie ścieżek transportowych i warunków brzegowych realizacji procesu pobrań materiału.
- Zdefiniowanie parametrów pracy oraz środka transportu realizującego pobrania
2. Symulacja pobrań materiałowych:
- Przygotowanie struktury danych procesowych.
- Import danych do systemu wraz z odpowiednią strukturą celem zasilenia algorytmów.
- Wybranie odpowiedniego algorytmu do realizacji zadania.
- Wygenerowanie najbardziej optymalnej listy pobrań.
Wyniki i wnioski – pobranie materiału z magazynu
Wyniki symulacji pokazują postępującą możliwość optymalizacji procesu pobierania materiału. W symulacji odzwierciedliliśmy 3 stany – pierwszy, który realizuje pobrania bez optymalizacji zakładając kolejność pobrań na bazie kolejności zleceń produkcyjnych (wynik symulacji 1000s). Dwa pozostałe używały odpowiednio algorytmu wyspowego oraz sortującego (550s i 200s odpowiednio). Optymalizacja przy użyciu symulacji pokazuje potencjał na poziomie aż 60% redukcji czasu operacji wstępnie zoptymalizowanego procesu.
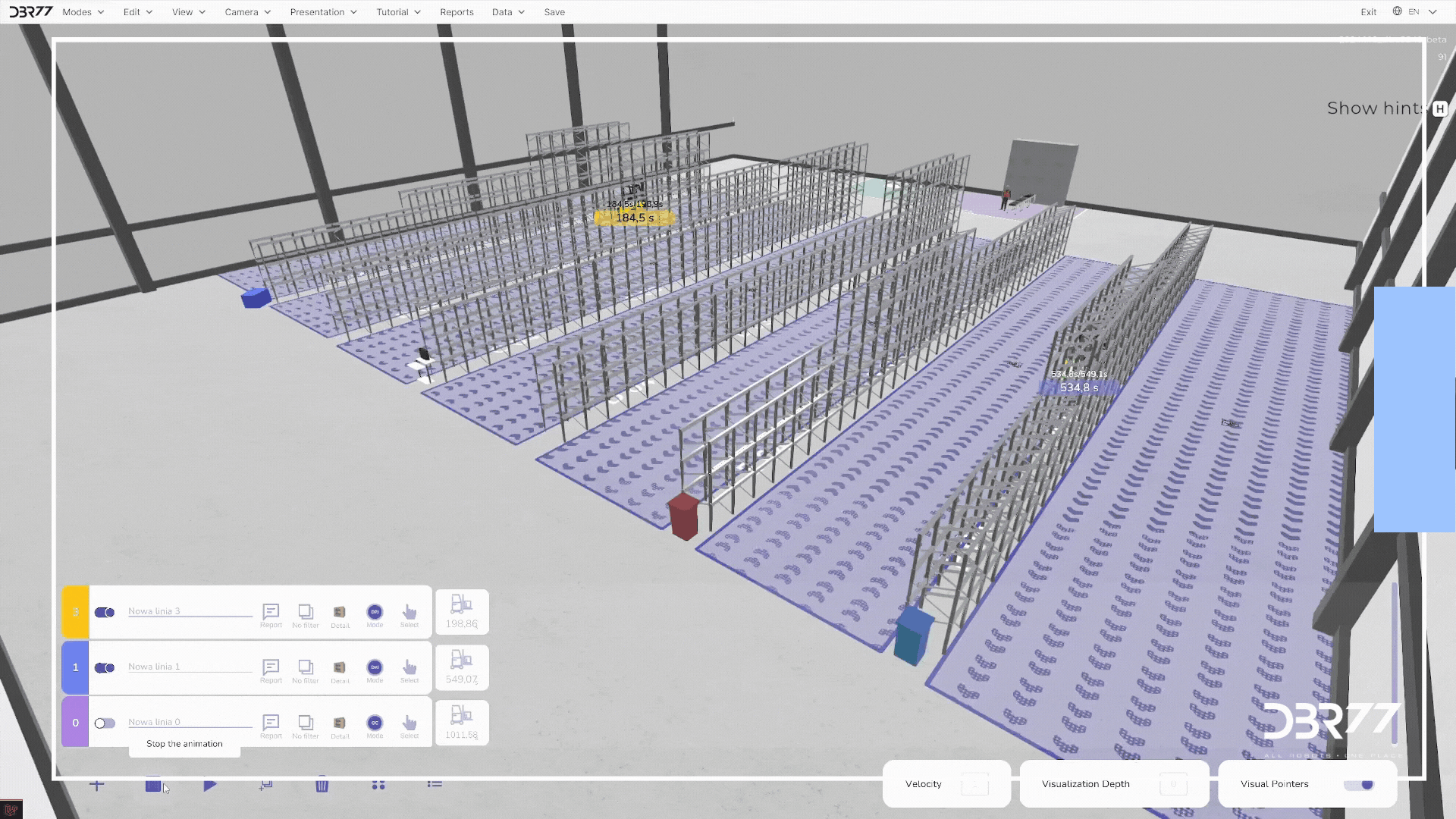
Korzyści dla firmy
Podsumowując, dzięki wykorzystaniu bliźniaka cyfrowego, firma w zaledwie kilka dni przygotowała symulację pobrań materiału na bazie aktualnych zleceń produkcyjnych oraz ma możliwość aktualizacji procesu w bardzo krótkim czasie – wystarczy zaimportować zaktualizowane zlecenie produkcyjne, a wybrany algorytm w kilka sekund znajdzie rozwiązanie. To jest szczególnie istotne w sytuacjach awaryjnych: brak surowca, operatora lub inne czynniki, które powodują konieczność zmiany produkcji.
Dlaczego Bliźniak Cyfrowy jest optymalnym rozwiązaniem?
1. Szybka możliwość odwzorowania procesu
Bliźniak cyfrowy pozwala na szybkie i dokładne odtworzenie rzeczywistego procesu produkcyjnego w wirtualnym środowisku. Dzięki zaawansowanym narzędziom do modelowania i wizualizacji, procesy mogą być odwzorowane z wysoką precyzją, co umożliwia lepsze zrozumienie i analizę ich funkcjonowania. Ponadto szybkie odwzorowanie skraca czas potrzebny na planowanie i implementację, co jest kluczowe w dynamicznych i konkurencyjnych rynkach.
2. Możliwość symulacji w oparciu o zdefiniowane algorytmy
Bliźniak cyfrowy umożliwia przeprowadzanie symulacji procesów produkcyjnych z wykorzystaniem zdefiniowanych algorytmów. Dzięki temu można testować różne scenariusze, przewidywać potencjalne problemy oraz optymalizować działanie systemu bez konieczności wprowadzania zmian w rzeczywistym procesie. W związku z tym, że symulacje mogą uwzględniać różne zmienne, takie jak zmiany w popycie, dostępność surowców czy awarie maszyn, możliwe jest lepsze przygotowanie się do rzeczywistych warunków operacyjnych
3. Łatwość aktualizacji założeń i wygenerowania nowych alternatywnych linii pobrań materiałowych
Bliźniak cyfrowy oferuje elastyczność w aktualizacji założeń i tworzeniu nowych alternatywnych scenariuszy. Dzięki temu w miarę jak zmieniają się warunki produkcyjne, założenia mogą być łatwo modyfikowane, a nowe alternatywne linie pobrań materiałowych mogą być szybko generowane. W konsekwencji zdolność do adaptacji pozwala na bieżąco reagować na zmiany w środowisku produkcyjnym, co zwiększa efektywność i elastyczność operacyjną.
PODSUMOWANIE
Podsumowując, wprowadzenie Bliźniaka Cyfrowego DBR77 umożliwiło optymalizację procesu pobierania materiałów na magazynie dla producenta z branży HVAC. Dzięki symulacji w środowisku cyfrowym, firma mogła dynamicznie generować listy pobrań dostosowane do zmienności produkcji, co znacznie usprawniło operacje magazynowe. Analiza wykazała, że czas potrzebny na pobranie materiałów można zredukować nawet o 60% dzięki zastosowaniu zaawansowanych algorytmów.
Zobacz też film o Bliźniaku Cyfrowym z konferencji DBR77 „(R)ewolucja Przemysłowa”: